Welding is the process of joining of two or more pieces of materials especially metals with the help of heat and pressure. Before the 19th century, there was mainly one type of welding that is forge welding which was mostly preferred by blacksmiths after arc welding and oxy-fuel welding. But due to eye-watching progress in welding technology, there are almost 35 advanced welding types present today.
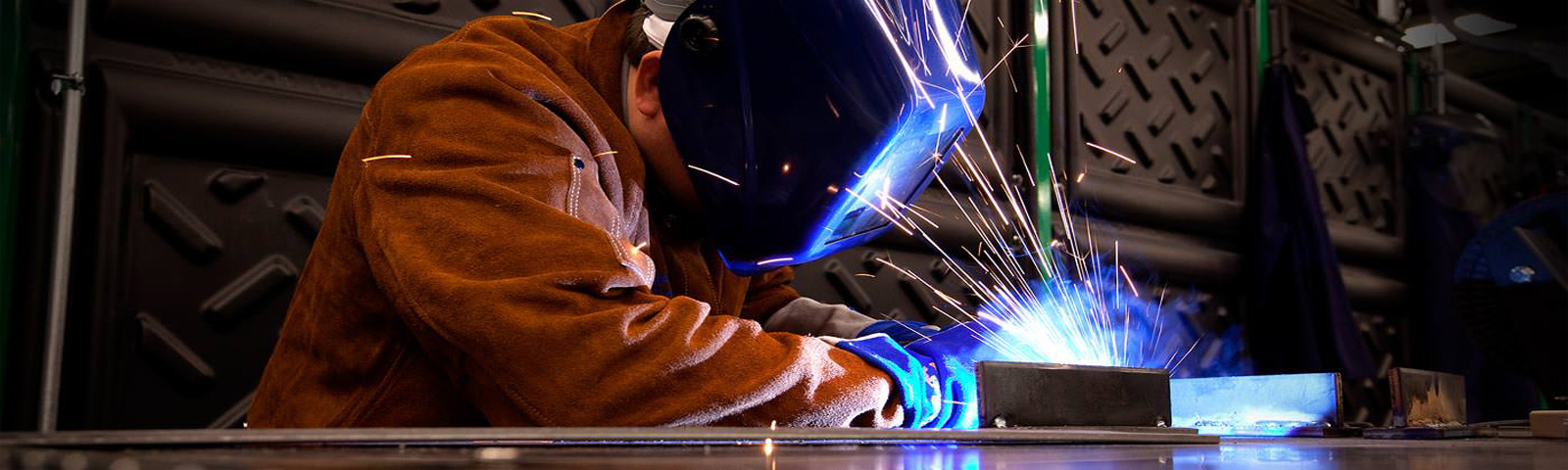
Types of Welding
The different types of welding process are
1) Gas Welding
(i) Air acetylene
(ii) Oxy hydrogen welding
(iii) Oxy acetylene
2) Arc Welding
(i) Shielded Metal Arc Welding (SMAW)
(ii) Gas Metal Arc Welding (GMAW) or (MIG)
(iii) Flux-Cored Arc Welding (FCAW)
(iv) Submerged Arc Welding (SAW)
(v) Gas Tungusten Arc Welding (GTAW) or (TIG)
(vi) Plasma Arc welding (PAW)
(vii) Atomic Hydrogen Welding (AHW)
(viii) Carbon Arc Welding (CAW)
(ix) Electroslag Welding (ESW)
(x) Electrogas Welding (EGW)
3) Resistance Welding
(i) Seam welding
(ii)Projection welding
(iii) Spot welding
(iv) Flash welding
(v) Resistance Butt welding
4) Radiant Energy Welding
(i) Electric or Electron beam welding
(ii) Laser beam welding
5) Solid-State Welding
(i) Cold Welding
(ii) Diffusion Welding
(iii) Explosive Welding
(iv)Forge Welding
(v) Friction Welding
(vi) Hot Pressure Welding
(vii) Roll welding
(viii) Ultrasonic Welding
Basically, there are three types of welding
1) Plastic Welding
It is also called as liquid-solid welding or pressure welding. Plastic welding is used in forge welding and resistance welding. This process includes combining small parts or pieces of metal. But before joining these small components they are strongly heated to achieve to a plastic state. After doing all these they are joined by applying external pressure.
2) Cold Welding
It is popularly known as solid-state welding which includes no application of heat but application of external pressure for the diffusion process. The parts are joined without contamination from atmospheric constituents. It is used in ultrasonic welding, friction welding and Explosive welding.
3) Liquid State Welding
In this technique metal at the junction point is allow to solidify after heating. In this filler materials are also supplied to the metal. It’s another name is Fusion welding. It involves gas welding, arc welding.
1) Gas Welding
(i) Air Acetylene Welding
It is a types of welding process in which heat is produced by combining mixture of acetylene and air. In this process there is an increase in temperature of about 2700 degree C. There is formation of weld point without application of heat or without using filler metals. In this type of welding only one tank is used which makes it less expensive and easy to handle.
If we see the working of Bunsen burner that is totally based on this air acetylene welding.
Applications:
• In case of leads having small area of cross section this method is used for welding.
• Also sheets of copper having small thickness are also welded by this process.
B) Oxy-Hydrogen Welding
In this process oxygen and hydrogen are used for fusing and cutting. The oxy-hydrogen flame produced in this process is typically of pale blue color. The temperature of this flame is about 2000 degree C. The workpiece is firstly heated and the melt bar fused in to make in the connection or joint. The time interval is not fixed for the completion of this process. It will vary from two minutes to five minutes depending on the size of sheets.
Disadvantages:
• There are more chances of leaking the gas in this process.
• It is more expensive than other alternative processes.
Uses:
• Melting of expensive metals.
• Polishing of acrylic glass surfaces.
• In metal manufacturing industries .
C) Oxy-Acetylene Welding
In 1903 Edmond and Charles Picard discover this welding type. This is one of the most important types of welding process commonly called as oxy-acetylene or oxy-fuel welding. The unique feature of this process is that it uses fuel gases such as hydrogen, natural gas, methane and oxygen to fuse and cut metal pieces. The flame temperature is about 3100 degree Celsius.
It involves two processes:
(i) Fusing or Welding
This process placed more emphasis on using welding torch to fuse metals. Tip of this torch is used to fuse metals. The torch consists of oxygen control unit, Fuel gas control valve and mixer.
(ii) Cutting or Slicing
Basically a cutting torch is used to crop the metal. Before cutting, metal components are heated up to ignition point by pressing oxygen blast lever present in the torch. Iron oxide and heat formation takes places after the reaction of metal with oxygen. The resultant heat is the deciding factor of the cutting process.
Uses:
1) For polishing in glass companies.
2) It is used in jewelry designing for the purpose of water welding,
3) To obtain a bright light in theatres.
Precautions:
1) Less than 1/7 the capacity of the cylinder should be used per hour.
2) Fuel leakage should be avoided.
3) Cylinders should be properly monitored and maintained.
2) Resistance Welding
It is the types of welding Processes mostly used in production sites for combining metal sheets and parts. The weld is made by passing a strong current through this junction to heat them and melt the metals. Factors affecting welding temperatures are electrode size, its specifications mean geometry, current, and interval of welding time. Small pools of molten metal are produced at the point of most electrical resistance as an electric current is passed through the metal.
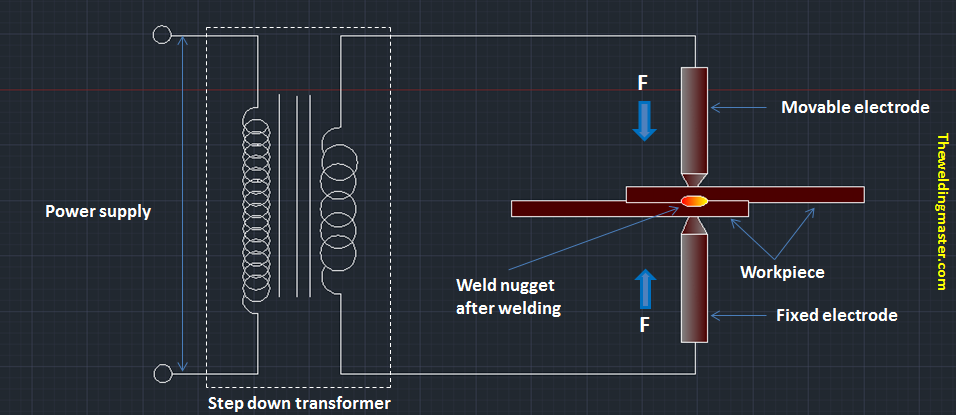
It mainly includes following processes:
(i) Spot Welding
Spot types of welding is a resistance welding method implemented to fuse the two or more metal hangers, sheets. Basically, two copper electrodes are used to clamp the metal sheets and then current is passed through these sheets. When current is passed to the sheets through electrodes, a gradually amount of heat starts generating as a result of strong electrical resistance at the contact point of electrodes and sheets. Due to rising temperatures, there is more dissipation of heat throughout the workpiece in just a second and then molten state grows to meet welding tips. So this is the process of spot welding.
Advantages:
• Filler materials are not required.
• It includes efficient energy use.
• Fast and easy automation.
Uses:
• It was used in making of BMW3 series.
• It is used in car industry to prepare a sheet of metal.
• It is also used in manufacturing process of batteries.
• It is also used in orthodontist’s clinic.
(ii) Seam Welding
It is an automated types of welding technique and it produces an efficiently durable weld. It generally produces a weld at the connecting surfaces of two similar metals. It includes two electrodes of copper and mostly these electrodes are disc-shaped and rotate as the material passes between them. The weld made from this process is stronger than the material from which it is made. It was formerly used for the construction of beverage cans.
(iii) Flash Welding
Flash welding doesn’t use any filler metals. There is a fix distance between metal pieces that are to be welded. On applying current to the metal, resistance is created between the spaces present among metals which generate required heat for the welding purpose.
Uses:
• It is used extensively in the railroad industry.
• It is also used to fuse aluminum, copper, and steel in various conductors.
(iv) Projection Welding
In these types of welding process, the weld is fixed to a particular position with the help of projections on the workpieces that we have to join. There is generation of heat at the projection in this process. Due to projection welding, there is a generation of internal cracks as well as an ugly look of metal. You need not take more safety measures while projection welding. Only simple goggles are required during this process.
(v) Resistance Butt Welding
This technique involves the application of heat and pressure to combine the two metal parts in localised area. It is generally used to make butt joints in wire as well as rods up to about 16 mm diameter. The larger and parallel surfaces of the pieces to be joined concentrate the strong heating at the interface. Current is passed through dies which in turn causes resistance heating of the weld area. This heating is larger in those areas where resistance is higher.
Advantages:
• It is super fast and clean process.
• It is better than flash welding due to its application over small components.
There are some precautions should be taken during this welding process:
• Eyes should be protected by wearing safety helmets.
• Leather gloves should be used.
3) Arc Welding
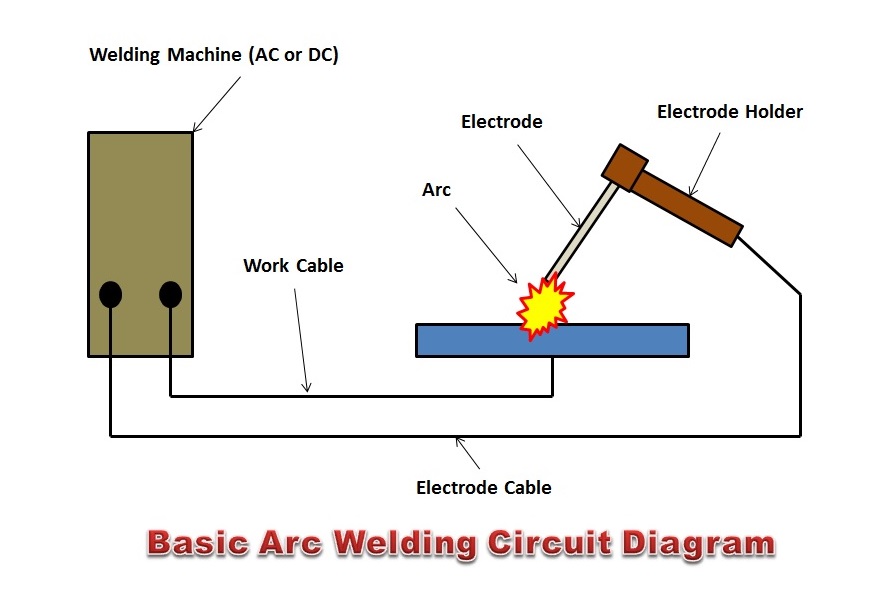
This process may be automated or manual. In these types of welding, metals are connected end to end with the help of electric supply which in turn results in sufficient amount of heat production for the welding purpose. This welded metal then allowed to solidify for their fusing. Direct current (DC) or alternating current (AC) can be used in this type. Mostly, a constant current supply is used for this process. Sometimes, the zone or area is covered with vapor or slag. There are two types of electrodes which are used in this process:- 1) Consumable electrodes (2) Non-consumable electrodes
(i) Shielded Metal Arc Welding (SMAW)
Shielded Metal Arc Welding is popularly called as Manual Metal Arc Welding (MMAW) or stick welding.
Its process and structure are similar to that of arc welding as it is a sub-type of arc welding. So as mentioned in arc welding in the same way an electric arc is created in this process. Electrode coated in core wire covered with flux. The temperature of about 6500 degree F is generated in this method. The molten metal is protected by gaseous oxides and nitrides with the gaseous shield so it is termed as Shielded Metal Arc Welding.
Uses:
• It is used in repairing of large machines.
• Usually used in pipeline welding.
If proper safety measures are not taken then it is a very dangerous process:
• Welding helmets, long sleeve clothes, and gloves should be wear during this process.
• Advanced welding masks can save your life from toxic fumes.
Advantages:
• Cheap cost machinery.
• Works on rough surfaces.
• Machinery involve in the process is easy to handle.
(ii) Gas Tungsten Arc Welding (GTAW) or (TIG)
It is also called as Tungsten Inert Gas (TIG) welding. It uses a non-consumable tungsten electrode for the welding purpose. Filler gas and shielding gases are used for protection.
To prevent contact between electrode and workpiece it is very necessary to keep a certain short arc length. An electric spark is created with the help of a generator and the distance of 1.5-3 mm is maintained between electrode and workpiece. Holding filler rod close to an arc is very harmful as it results in the melting of filler rod before making any contact with the weld pool. At the end of the weld, there is the formation of a solidified hole shaped or simply crater cracks.
Uses:
• This type of welding process is extensively used in aerospace welding.
• In the manufacturing of motorcycles and bikes.
Advantages:
• Higher deposition rates.
• Large and good quality of welds.
• Very thin materials can be easily welded.
(iii) Gas Metal Arc Welding (GMAW) or (MIG)
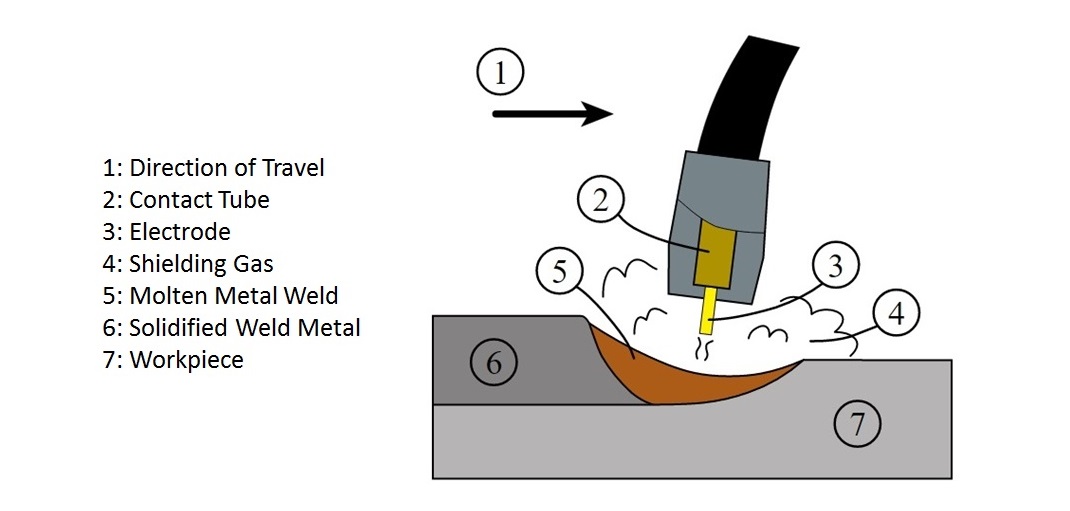
It is mainly referred by its subtype Metal Inert Gas Welding (MIG). It is not a 100% manual process. It can be semi-automatic or fully automatic. It was originally implemented to aluminium as well as non-ferrous metals but soon it is applied to steels because of its quick welding time compared to similar processes. In this process, the welder has to use one hand for holding the torch and there is a filler wire in the other hand. This is a very simple and easy technique of welding and generally require a span of one week for learning it. It’s working procedure is almost similar to that of arc welding. The shielding gases are carbon dioxide or the mixture of carbon dioxide and argon-carbon dioxide.
It is useful in the fabrication and automobile industry.
Advantages:
• Reduce heat inputs
• Easy to learn and use
• Efficient electrodes
(iv) Flux Cored Arc Welding (FCAW)
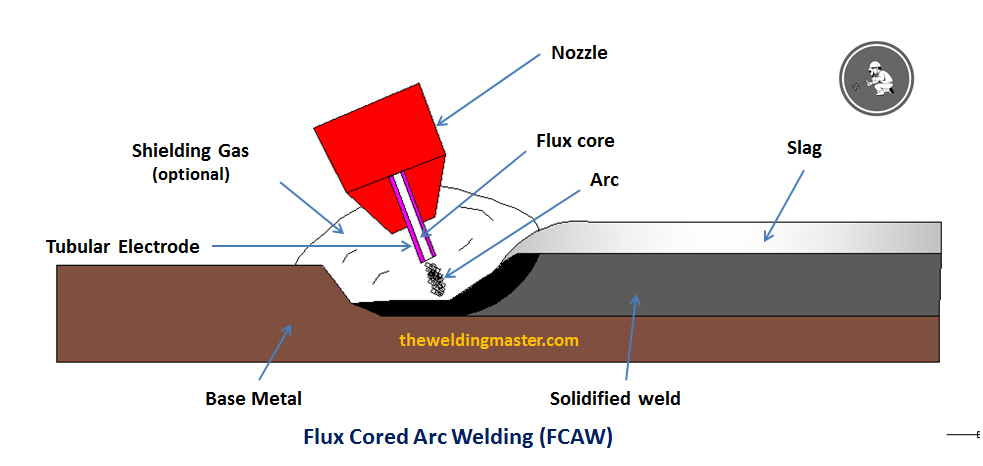
It is similar to GMAW only it requires continuously used fed electrode and uses tabular wire filled with flux. There are two types of FCAW -one uses shielding gas while others don’t require any shielding gas. FCAW with no shielding gas is made by a tubular consumable electrode containing flux core. It is attractive due to its portability and good penetrating power into metal. Another type of welding that uses shielding gas is termed as dual shield welding. This FCAW was purposefully developed for welding thicker metals and structural steels. The biggest advantage of this type of FCAW is that it produces high-quality welds than SMAW or GMAW.
Advantages:
• It is a perfect, all position process.
• Less skills required as compared to SMAW.
• No requirement of shielded gas.
Uses:
• Used in quick automotive machines.
• Welding of stainless steel and nickel alloys.
(v) Submerged Arc Welding (SAW)
In SAW types of welding process, there is a prevention of welded zone from atmospheric contamination by submerging under a flux that contains lime, silica and calcium fluoride. The molten conductive flux provides a current path between the electrode and the workpiece. In the market there are semi-automatic guns containing pressurized flux are available. The arc length is kept constant by the self-adjusting arc principle. Arc length is inversely proportional to the voltage increase.
Uses:
• In the corrosion-resistant layer of steel.
• In vessel construction, it is mostly used.
• The welding process containing alloys of nickel and low metals.
Advantages:
• More than half of the flux can be reuse and recycle.
• The welding process is very deep.
• Production of welds that are ductile and resistant to corrosion.
(vi) Plasma Arc Welding (PAW)
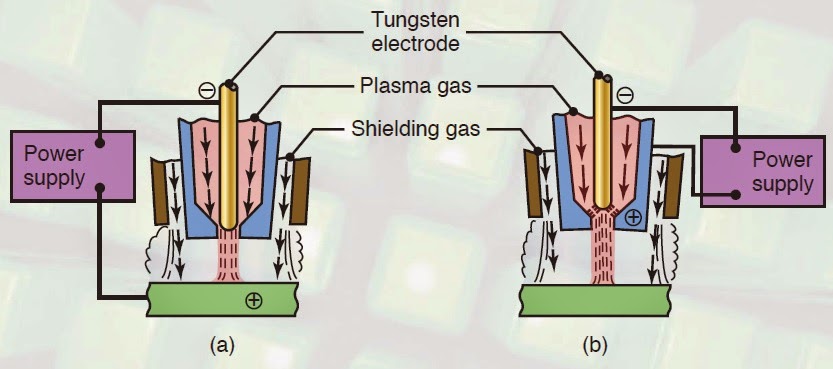
PAW is a type of welding that has a similar process to that of GTAW. The only difference is that in PAW, the position of the electrode is in the body of the torch as well as plasma arc is separated from shielding gas protection. There is special use of plasma torch in this process for cutting and welding. For shielding purpose argon is mostly prefer compared to helium. Helium is in process when there is a requirement of broad heat input pattern. There are at least two separate gas flows are needed in PAW.
Some plasma processes are:
1) Plasma arc cutting
2) Plasma arc spraying
3)Plasma arc surfacing
(vii) Atomic Hydrogen Welding (AHW)
In the presence of a shielding environment of hydrogen, arc is applied between two tungsten electrodes in AHW. Due to this arc, there is an increment in temperature up to 4000 degrees C.
The arc is used well apart from the workpiece. By changing the distance between arc and the workpiece the energy is controlled in AHW. Nowadays gas metal arc welding is used rather than AHW due to the availability of cheap inert gas. The filler metal may be used in this process. This method is also called as arc-atom welding. The torch used is atomic hydrogen torch or Langmuir torch.
(viii) Carbon Arc Welding (CAW)
In CAW types of welding techniques, an arc is heat between carbon electrode and workpiece to produce the merging of metals. This arc produces a temperature of about 3000 degree C. At this temperature separate metal forms a bond and welding takes place. GTAW, PAW, AHAW have replaced CAW in this modern world. There are also 2 subtypes in CAW:
(1). TCAW (Twin Carbon Arc Welding)
In Twin Carbon Arc Welding arc is placed between 2 carbon electrodes
(2). CAW-G (Gas Carbon Arc Welding)
It is Gas Carbon Arc Welding. Generally a filler metal is used for the bondage in workpieces.
(ix) Electroslag Welding (ESW)
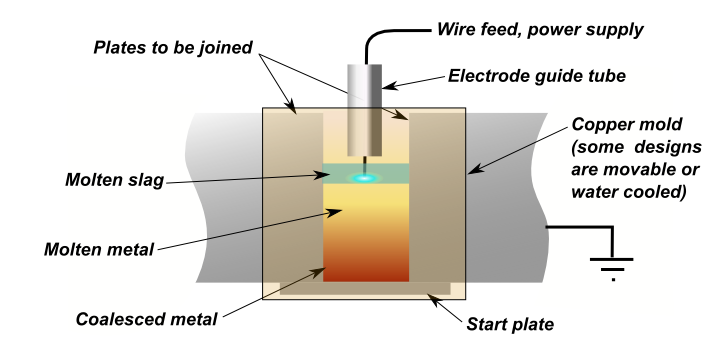
Mostly, electroslag types of welding are used for welding of thick materials. Due to the dissimilarity in arc positions there exist a difference between electroslag and electrogas welding process. An electric arc is hit at the weld location and additional flux is added until the slag extinguishes the arc. It is used to combine steel sections that are very thick. It is also implemented on structural steel plates. It requires a current of about 600 A and a voltage of about 45-55 V.
Advantages:
• Very large deposition rate of about 20 kg per hour.
• Safe and efficient process.
• Less requirement of labor work of high skills.
(x) Electrogas Welding (EGW)
There is no use of shielding gas and also no pressure is applied. The only difference between EGS and EGW is that arc in EGW is not quenched. It is implemented to most of the steels including low and medium steels. It requires the current ranging from 100 to 800 A and voltage ranging from 30-40 volt. Carbon dioxide is widely used as shielding gas. A large amount of molten metal is used in these types of welding processes which increases the safety measures that have to be taken care of properly. It is advisable to wear a helmet during this process.
Uses:
• In shipbuilding processes
• In the development of storage tanks.
(xi) Stud Arc Welding
It is the most extensively used fastening process. It can weld any type of metal stud to the workpiece. There is a requirement of DC power supply, a welding gun, and metal fasteners. There is no much pressure requirement in this method.
Advantages:
• It is used in jewelry production.
• It is used in pumps, motors, and electronic gadgets.
• Used in household utensils and hardware.
(4). Radiant Energy Welding
In radiant energy welding, we use radiant energy produced for the welding of two metal pieces together.
(i) Laser Beam Welding
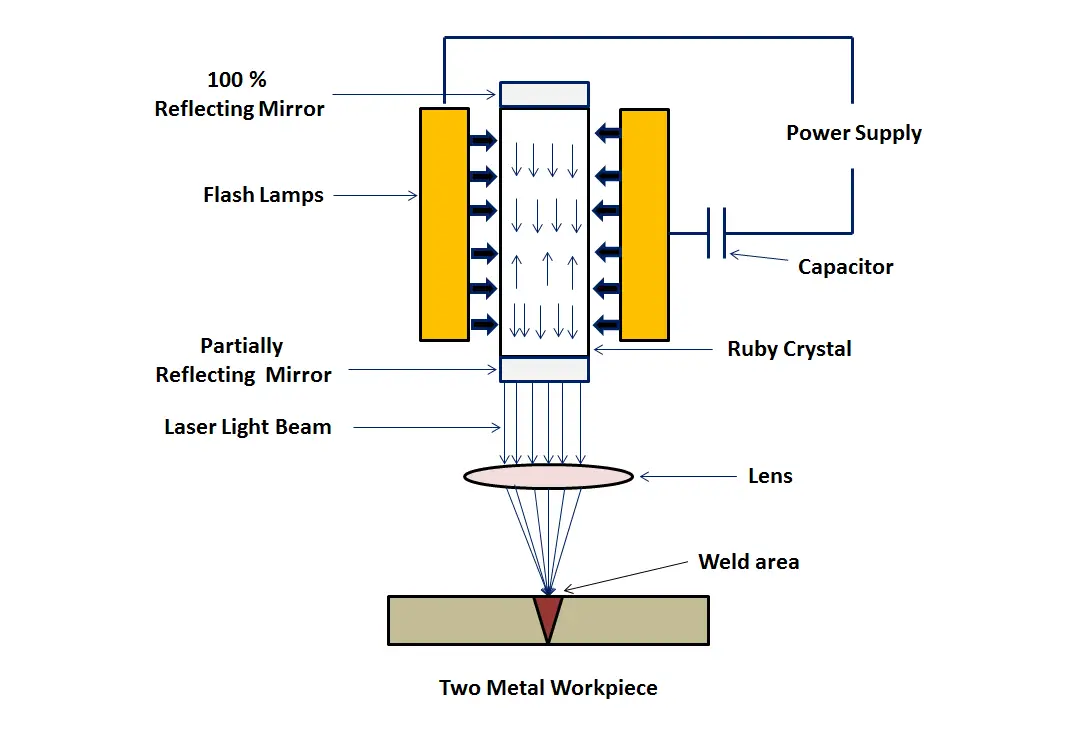
It is a process of joining two or more pieces of metal with the help of a laser beam. The weld of this type is formed as a result of a light beam falling on the metal. This process takes place in a few seconds. As a laser beam is monochromatic it will produce a large amount of heat after hitting the metal surface. This laser beam contains highly concentrated energy due to its coherency and single frequency. For welding purposes, there is a need for sharply concentrated rays. The size of the laser spot can be small as 0.076 mm. The lasers which are used for cutting purpose in these types of welding have very high cost.
Advantages:
• Easy to use in an open environment.
• Highly efficient in welding small components.
• There is no need for contact with any material.
(ii) Electron Beam Welding (EBW)
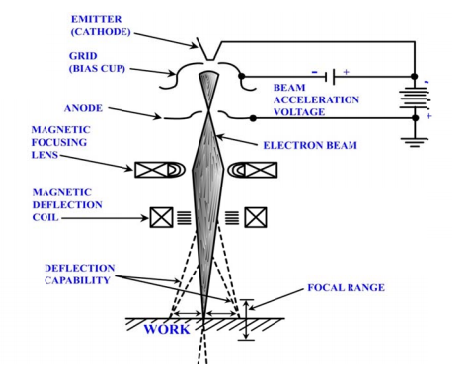
EBW is an advanced type of welding technique in which a beam of highly energetic electrons is focused on the metals to be combined. In this process, the kinetic energy of these highly accelerated electrons is converted into heat energy. Due to this reason the workpieces melt and flow upon incident of electron beam.
The machine uses for this purpose consist of four compartments:
• Electron gun: Generating highly accelerated electrons.
• Vacuum chamber
• Control and power supply system.
• Electric and magnetic field generator.
(5). Solid-State Welding
It is a collection of welding methods that produce merging at temperature especially below the melting point of base metals that are to be joined. The Various types of welding process that come under solid-state welding are described below:
(i) Cold Welding
This Welding technique uses pressure at room temperature to produce coalescence of metals. Welding is achieved by applying high pressure on clean materials. Cold welding is usually implemented to combine the ductile metals. For instance, aluminum and copper can be joined together by cold welding.
(ii) Forge Welding
In this technique, there is permanent deformation at the interface due to the application of sufficient pressure and resulting in a coalescence of metals by heating them. It was formerly called hammer welding. This process is of minor use in industry today.
Uses
• It is used in the manufacturing of prison cells and shotgun barrels.
• Also in the manufacturing processes of swords and cookware.
(iii) Diffusion Welding
Diffusion welding is solid-state types of welding which is capable of joining similar as well as dissimilar materials. It involves no filler metal. If the metal has strong oxide layers then diffusion welding must be done in a vacuum or in the presence of inert gas conditions.
Uses:
• It is used in electronics and the nuclear industry.
• Metals like titanium, zirconium can be easily melted with the help of this process.
• In military aircraft, there is a need for less expensive metals due to this process.
Advantages:
• Tensile testing can be easily done
• Easy processing of similar as well as dissimilar metals.
(iv) Explosive Welding (EXW)
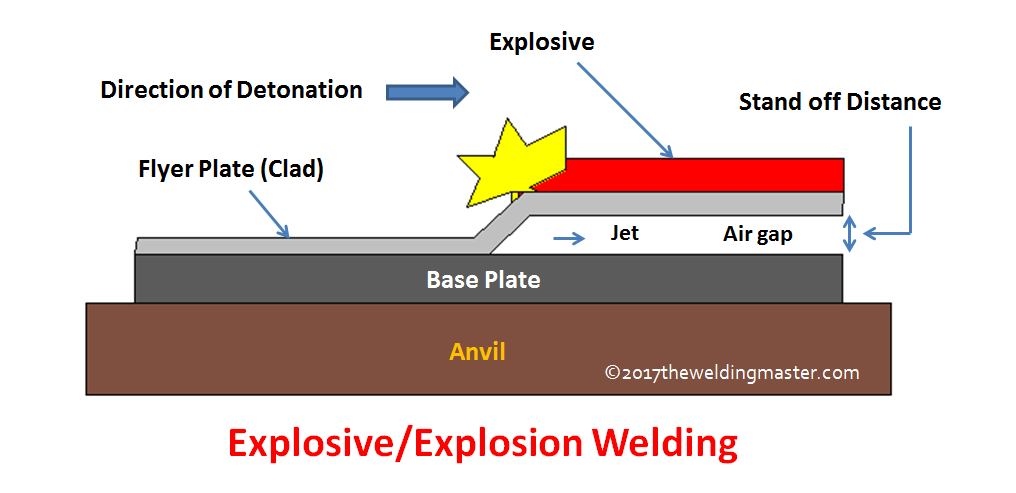
EXW was developed during world war 2. It is mostly based on metallurgical bonding. With the help of chemical explosives, one of the parts is accelerated. This method is used to develop plates and tube sheets. It is used in small shops for joining a cooling fan.
Advantages:
• Easy bonding between two metals that cannot be welded by other alternatives.
• Quick welding of large areas.
• Welding is efficient and clean.
(v) Friction Welding (FRW)
In FRW there is heat generation due to friction between workpieces. Friction surfacing is the procedure involved in FRW where a substrate is protected with a coating substance. It is used with thermoplastics.
Advantages:
• They are melt free.
• Relative motion between workpieces cleans their surfaces.
• In aerospace, it is useful to join dissimilar materials like aluminum with steels.
(vi) Hot Pressure Welding
It is the subtype of solid-state types of welding processes in which welds are produced between two connecting metals. There is a generation of plastic deformation and there is no requirement of filler material in this technique. A pressure of 40-70 MPa is applied during the whole process. Heat may be generated with the help of eddy currents.
Advantages:
• Less expensive machinery.
• Quality and quick weld production.
(vii) Roll Welding
It is the resultant of flat rolling of metal sheets. The two or more metal pieces passed between two rollers and there is large pressure applied on rollers to reduce the effective metal thickness. To improve the quality and strength of weld it should be pre-heated before welding. It should be performed in quite warm conditions.
Uses:
• In refrigerators, there are heat exchangers that are created from this technique.
• Used in efficient cladding of metal sheets.
(viii) Ultrasonic Welding (USM)
It is the most advanced type of welding method, in which high-frequency ultrasonic vibrations are applied to workpieces for the formation of weld. It is widely used for plastics and combining dissimilar materials. The frequency of ultrasonic rays varies from 15kHz-70kHz.
Uses:
• Combining thermoplastics
• Used in motors, capacitors, transformers.
• In microcircuits, this is the most dominant welding technology.
Conclusion
So these are some Types of welding due to which we get all the perfectly welded automobiles and machines today. In the future, there must be an advancement in today’s welding techniques to make our lives better and happy.