Are you interested in knowing different welding electrodes? Then this article is surely for you. In this article, you will get deep knowledge about welding electrodes, their types, and many more. So, what are you waiting for? Let’s get started.
What is Welding Electrode?
A welder needs an electrode to generate an electric current to do arc welding. In welding, an electric current is conducted through an electrode which is used to join the parent metals. When you keep the electrode tip near the parent metal electric current jumps from the electrode tip to the parent metal. The main purpose of electrodes used in welding is to create an electric arc. These electrodes can be positively charged anode or they can be negatively charged cathode.
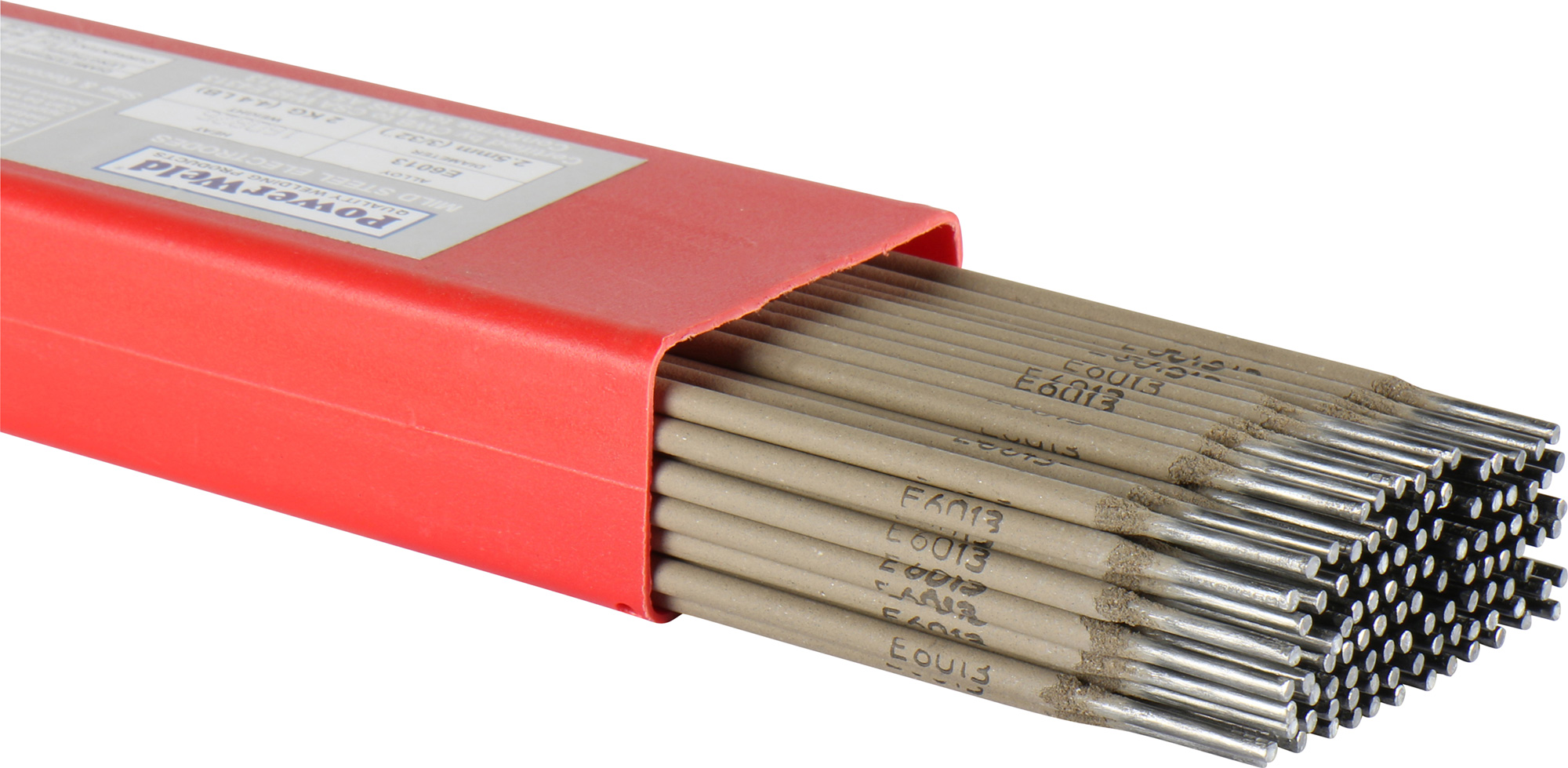
Factors that you must consider before selecting welding electrodes:
- The electrode rod should have greater tensile strength than the parent metals.
- You have to consider joint design, shape, specifications of base metals and welding positions.
Types of Welding Electrodes
Basically, depending on the process there are two types of welding electrodes:
- Consumable Electrodes
- Non-Consumable Electrodes
1. Consumable Electrodes
Consumable electrodes have a low melting point. These types of welding electrodes are preferred to use in Metal Inert Gas (MIG) welding. For making consumable electrodes, materials such as mild steel and nickel steel are used. The one precaution that you must take is to replace consumable electrodes after regular intervals.
The only disadvantage of using such electrodes is that they don’t have a large number of industry applications but at the same time, they are easy to use and maintain.
Consumable electrodes are categorized as:
- Bare Electrodes
- Coated Electrodes
(i) Bare Electrodes
Bare electrodes are electrodes without any type of coating and mostly used in applications where there is no need of coated electrode.
(ii) Coated Electrodes
Coated electrodes are classified according to the coating factor. Coating factor is the ratio of the diameter of the electrode to the diameter of the core wire.
So, the following are sub-types of coated electrodes:
- Light coated electrodes with coating factor of 1.25. Light coating applied to electrodes helps to remove impurities such as oxides and phosphorous. Light coating also helps in enhancing arc stability.
- Medium coated electrodes with coating factor of 1.45.
- Shielded arc or Heavily coated electrodes with coating factor ranging between 1.6 to 2.2. These electrodes have a proper and well defined composition. The heavily coated electrodes are designed in three types – electrodes with cellulose coating, electrodes with mineral coating, and electrodes with coating of both cellulose as well as mineral coating.
Also Read:
- Types of Welding Process – Everyone Should Know
- Difference Between MIG and TIG Welding
- Different Types of Welding Joints
2. Non-Consumable Electrodes
These types of welding electrodes are also referred to as Refractory electrodes. There are again two sub-types of non-consumable electrodes:
- Carbon or Graphite Electrodes: It is made up of carbon and graphite and mostly used in the applications of cutting and arc welding.
- Tungsten Electrodes: Basically, it consists of tungsten as the name itself suggests and it is a non-filler metal electrode.
As the name suggests, these types of welding electrodes are not consumed in the entire welding process or we can say more appropriately that they do not melt during welding. But practically, due to the vaporization and oxidation processes taking place during welding there is a little bit reduction in the length of the electrode. The non-consumable electrodes have high melting point and are unable to fill the gap in the workpiece. Non-consumable electrodes are made from materials such as pure tungsten, graphite or carbon coated with copper. The melting point of carbon is 3350 degree Celsius and that of Tungsten is 3422 degree Celsius. Non-consumable electrodes are used in Tungsten inert gas welding (TIG) and carbon arc welding.
Important Characteristics of Non-Consumable Electrodes:
- While using non-consumable electrodes you have to use shielding gases. The shielding gases are inert gases and the reason behind to use them is to protect the welding area from oxygen and surrounding atmosphere.
- The non-consumable electrodes are usually made as cathode and the workpieces as anode.
Classification of Welding Electrodes
This classification is based on practical approach towards using and selecting welding electrodes. The American Welding Society has classified electrodes in different formats for proper understanding of different electrodes easily and to identify them comfortably.
Suppose we consider the electrode named as E6018-X
- Here the E indicates that this is an electrode.
- The consecutive two digits after the letter E gives you the tensile strength of the electrode. This tensile strength is measured in psi and this strength is 1000 times the given number. That means here this tensile strength of the given electrode is 60,000 psi.
- Here 1 indicates the welding position. The welding position is indicated by 1,2 and 4.
1 indicates flat, horizontal, vertical position.
2 indicates flat, horizontal position.
4 indicates flat, horizontal, vertically downward position.
- The number 8 gives you information about the type of coating and current used. It also tells about the penetration of electrode means the electrode may penetrate deep, low, medium.
- The X in the E6018-X tell us about the additional specifications of an electrode. Here the term X is not always mentioned. It is used only when an electrode has some additional features. This classification is applicable to mild steel coated electrode. If you consider other types of electrodes, the classification will be same but only the feature represented by X letter may vary.
- Some additional properties represented by letter X:
-1: It indicates that the electrode is more ductile and has high toughness.
-M: It is comfortable for military applications and low moisture content.
-H4, -H8,-H16: All represents maximum diffusible hydrogen limit measured in millimetres per 100 Grams. For instance, -H4 = 4 mL per 100 grams.
Precautions that you must take while handling welding electrodes:
- You must always keep electrodes dry.
- As moisture destroys electrode coating and is very harmful for electrodes. So, as soon as electrodes get dried, you must keep welding electrodes in moisture free environment. There are various containers available which gives you moisture free experience.
- Last but not the least, never bend the electrodes as bending can harm electrode coating.
Conclusion
In short, after reading this article you must get clear information about different types of welding electrodes, its classification system of welding electrodes, etc. Hope this article will help you. Share this knowledge maximum because sharing is caring.