Welding is an important aspect in the field of engineering as well as in the field of machining. In this digital world, there are many welding processes that are in practice. They can be manual processes or fully automatic. Today, we will learn the entire concept of forge welding. So, stay tuned.
What is Forge Welding?
Forge welding is a type of solid-state welding process in which two metal pieces are first heated and then, they are joined. During this welding technique, a process of hammering is also carried out. It is considered the oldest method of welding. In the previous century, this welding process was done mostly manually. But as technology is evolving day by day, automatic forge welding has been invented.
During any welding process, it is highly advised to wear protective gear such as welding helmets, gloves, Jackets, Glasses, welding Boots etc,. This will protect you from sparks, and heat produced During welding.
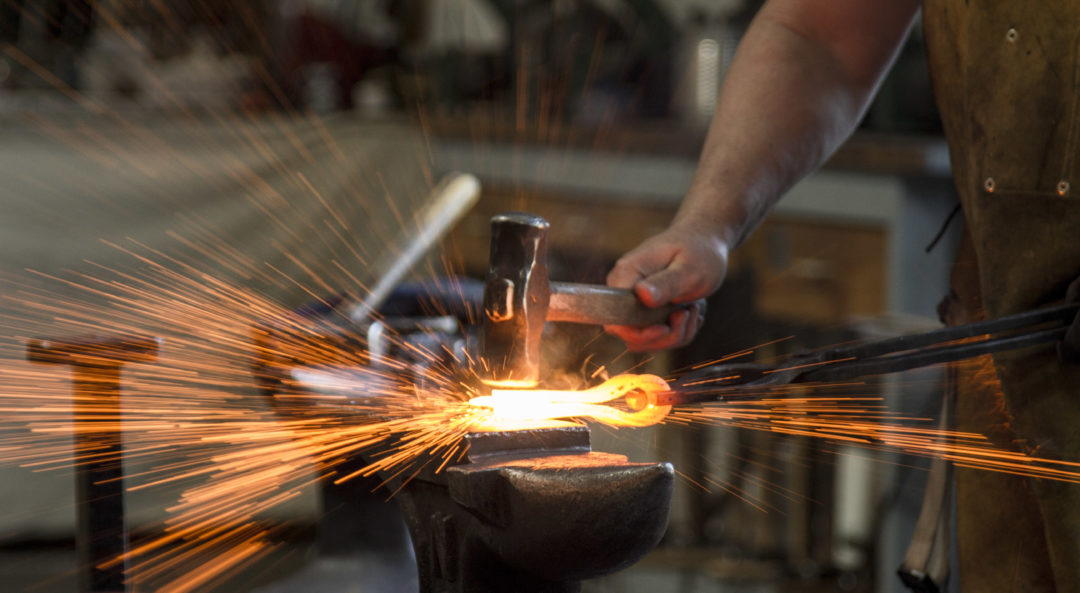
The History Behind It
This welding technique is the first type of welding process that ever has been discovered by human beings. It was founded around 1800 BC in the Anatolia. In today’s world, Turkey is considered as the major component of the Anatolia.
Also Read:
- Electron Beam Welding Process – Equipments, Working Principle with Diagram
- Explosive Welding – Equipment, Types, Working, Advantages and Disadvantages with Application
- Thermit Welding Process – Main Parts, Working Principle with Application
Working Principle Forge Welding
In this welding technique, two metal pieces are heated below their melting temperature. You can also say that the metals are heated in such a way that they should reach their plastic condition. Generally, this heating temperature is below 1000 ºC. But for some metals, this heating temperature may be above 1000 ºC. This heating temperature may vary from metal to metal. So, here care should be taken that you must not heat the workpieces or the metal above its melting temperature and just heat it in such a way that it will reach its plastic condition.
What after the heating of the metal pieces? After the heating process is done, a process of hammering is carried out. The metal pieces are hammered in such a way that they will undergo a process of diffusion. Sometimes, instead of hammering, an external force is applied to the metal pieces so that they will join perfectly. Whether you apply the external force or you do the hammering process, care should be taken is that there must be the formation of a strong weld at the joint. It is possible that while this welding technique, oxidation at the weld surface may take place. So, to prevent this oxidation, a flux is used.
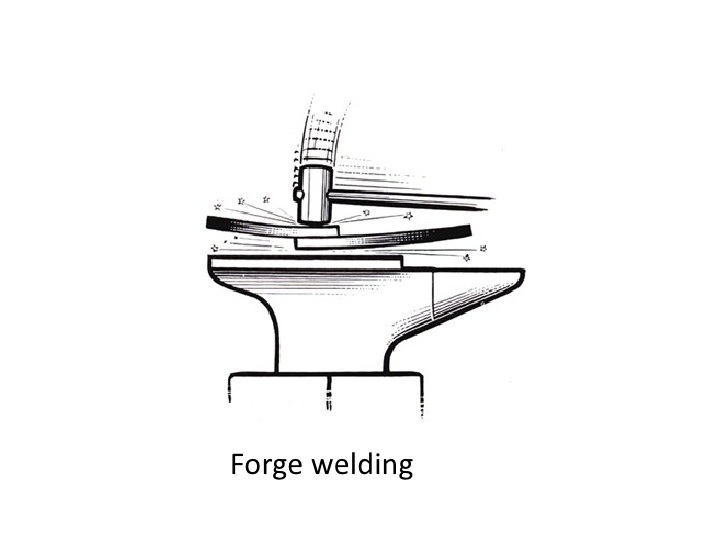
Above image will help in understanding the exact working of this welding technique. Here, you can see the two metal pieces are first gets heated, and then the hammer is used to join the two metal pieces.
For a better understanding of forge welding watch the video:
Following are some temperature variations for different metals:
- For Wrought Iron: In the case of wrought iron, the heating temperature must be just below 1290 ºC
- For High Carbon and Alloy Steel: For this, the temperature must be in the range of 1100 ºC to 1140 ºC
- For the Soft Carbon Steel: The temperature must be between 1250 ºC to 1300 ºC.
Following are the tools or equipment that you must have during Forge welding:
- Hammer
- Brass
- Black Smith Gauge
- Flux
- Anvil
Also Read:
- Friction Stir Welding – Working Principle, Advantages, Disadvantages with Application
- Ultrasonic Welding Process – Working Principle, Parts, Advantages and Disadvantages with Application
- Resistance Welding – Principle, Working and Application
Application of Forge Welding
- Such a welding process is used for the manufacturing of the crankshaft.
- It plays an important role in the aerospace industry. Most of the parts of an airplane are joined by the forge welding
- Many of us like the shape as well as structure of shotgun barrels. And this welding technique is also used in the production of shotgun barrels.
- The bicycles that we ride on our daily basis are also being manufactured with the help of this welding technique.
- As above mentioned, nowadays the concept of automatic forge welding is discovered. Such welding is used in the automobile industry. All the types of machines related to farming are developed with the help of such welding techniques.
As this welding technique is widely in use, there are many advantages as well as disadvantages of it. Let’s have a close look at some of its advantages:
Advantages of Forged Welding
- As the purpose of any welding process is to obtain the best quality weld at the joint, this purpose is achieved by this welding process. It gives us a clear joint easily and quickly.
- During this process, a little amount of noise is created and due to this, forge welding is considered as the best among all the welding processes.
- Unlike other welding processes, this welding technique requires no filler metal.
- Do you want to produce welds with high strength? Then, this is the perfect welding process for you. It gives rise to welds of higher strength along with the neat and crystal-clear weld.
Disadvantages of Forge Welding
As everything has its advantages as well as its disadvantages. Forge welding has also its disadvantages:
- During this welding process, you must have skilled labor. Its operation is quite difficult, so you must have the proper skills to carry out this process.
- This welding process is considered as the slow welding process as manually doing this welding is a quite time-consuming process.
- Sometimes there are chances that the contamination of the weld with the coke may take place. Care should be taken so that such contamination will not happen.
The Biggest mistake that people do while this welding technique:
While implementing this welding process, people should not try to hammer too hard. Hammering too hard will affect the entire welding process and you will not get the high-quality weld at the joint that you wanted.
Conclusion
This is all about forge welding. In this article, we come across the principle, advantages, disadvantages as well as applications of this incredible welding technique. Hope you got this concept. If you have any doubts feel free to comment below. We are always here to help you!