Definition
Submerged Arc Welding (SAW) is the most commonly used welding process in which the welding arc is travels beneath a blanket of granular flux. In this welding technique, a consumable solid or tubular electrode is fed continuously to the weld zone. Simultaneously a blanket of granular fusible flux is poured on the weld zone which submerges the welding arc and protects it from atmospheric contamination.
The granulated flux contains silica, lime, calcium fluoride, manganese oxide, and other compounds. When the flux is molten, it becomes conductive and provides a current path between the electrode and the workpiece. The thick layer of flux covers the molten metal completely and prevents the spatter (cover with drops or spots of metals) and sparks as well as covers up the intense ultraviolet radiation fumes produced during the process.
- This welding process was discovered in 1935. It was originally developed and patented by Kennedy, Jones, and Rothermund.
- SAW can be operated in semi-automatic (handheld) or in automatic mode. But normally it is operated in automatic mode.
Power Supply
DC or AC power source can be used for SAW. And for multiple electrode systems, a combination of DC and AC are commonly used.
The current range utilized in the process is 300 A to 2000 A. for multiple arcs, a current of up to 5000 A has also been used.
Main Parts or Equipment
The main parts or equipment used in the submerged arc welding (SAW) process are
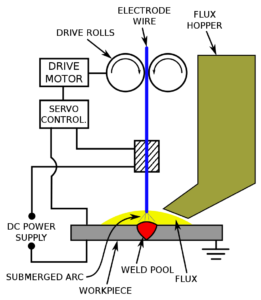
Image Source
- Welding head
- Flux hopper
- Flux
- Electrode wire feed unit
- Electrode
- Flux recovery unit
Also Read:
- How Ultrasonic Welding Works ?
- Friction Stir Welding – Working Principle, Advantages, Disadvantages with Application
- Explosive Welding – Equipment, Types, Working, Advantages and Disadvantages with Application
- Welding head: It is used to feed flux and filler metal to the joint to be weld.
- Flux hopper: Here the flux is stored and delivered to the welding joint. It controls the rate of deposition of flux to the welding joint.
- Flux: The weld arc is shielded by granular flux. It consists of lime, silica, manganese oxide, calcium fluoride, oxides of calcium and other compounds. It fed into the weld zone by gravity flow through the nozzle of the welding head.
When it is molten, it becomes conductive and conducts the current in between the electrode and the work. The thick layer of granular flux covers the molten metal completely and prevents the spatter and spark as well as cover up the ultraviolet radiations and fumes which is characteristic of the shielded metal arc welding (SMAW) process. The lower part of the flux gets melted and forms a slag on the weld pool. It is removed after the welding process gets completed. The upper part of the flux acts as an insulator and promotes deep penetration of heat to the workpiece.
- Electrode wire feed Unit: It provides a continuous feed of electrode wire to the welding joint. It consists of a reel on which the electrode wire is wounded.
- Electrode: Submerged arc welding uses a consumable electrode which is a coil of bare round wire of diameter 1.5 mm to 10 mm. It is fed automatically through the welding gun. The composition of the electrode depends upon the material being welded. The electrodes are available to weld high carbon steel, mild steel, low and special alloy steels, stainless steel, etc. The electrodes are usually coated with copper to prevent rusting and increases electrical conductivity. They are available in straight length and in coils.
- Flux recovery unit: It collects the unused flux left after welding. And after recovery, it is used again for the welding.
Working of Submerged Arc Welding
- In submerged arc welding, first, the flux starts to deposit on the joint to be welded. When the flux is cold, is act as an insulator.
- The arc is initiated by touching the tool with the workpiece. The arc struck always remains under a thick layer of flux. The heat generated by the arc melts the granular flux.
- The flux once melted by heat of the arc, it becomes highly conductive. The current starts to flow in between the electrode and w/p through the molten flux. The flux that is in contact with the atmosphere, which we can see remains granular and can be reused again. The lower melted flux changes to slag and it is a waste that is removed after the welding process completes.
- At a predetermined speed, the electrode from the reel is continuously fed to the joint to be welded. If welding is semi-automatic, the welding head is moved manually along the joint. In an automatic welding setup, a separate drive is used to move either the welding head over the stationary job or job rotates/moves under the stationary welding head.
- By using the principle of self-adjusting arc the arc length is kept constant. If the arc length decreases, the voltages of the arc increases and this increase the arc current. Due to this the burn-off rate increases and causing the arc length to increase or lengthen. The reverse phenomena occur in the case the arc length increases more than the normal length.
- For controlling penetration and to support large amounts of molten metal a backing plate of steel or copper may be use.
Also Read:
- How Laser Beam Welding Process Works?
- What is Underwater Welding and How it works?
- Flux Cored Arc Welding (FCAW) Process – Main Parts, Working, Advantages and Disadvantages with Application
Advantages
- It has a high deposition rate. The deposition rate reported is over 45 Kg/h.
- It exhibits deep weld penetration.
- Thin steel sheets can be weld at high speed upto 5 m/min.
- Minimum arc light and welding fumes are emitted.
- It is suitable for both indoor and outdoor works.
- Since the arc is always covered with a blanket of flux, so the chance of formation of spatter is zero.
- It has the ability to form welds in thick plates in a single pass with normal equipment.
- It produces high-quality welds without any difficulty.
- The weld produced by the SAW process is of high quality, ductile, uniform, corrosion resistance and possesses good impact value.
- Almost 50 to 90 % of the flux utilized in the process is recoverable, recycled and reused.
Disadvantages
- It is limited to thick materials.
- It is limited to weld in flat and Horizontal position only.
- It can weld only ferrous (steel or stainless steel) & some nickel-based alloys.
- Flux and slag present in the process leads to health and safety concern.
- Backing strips are required for proper root penetration.
- SAW is limited to long straight seams or rotated pipes or vessels.
Application
- The submerged arc welding process is used to weld stainless steel, carbon steel, low alloy steels, & nickel-based alloys.
- It is used to weld pipes, vessels, and boilers.