Friction Welding (FRW) is a solid-state welding process which means that in this process heat is not provided from outside the system and no molten state of metal is present in this process. In this welding, process heat is generated by mechanically induced friction by sliding a workpiece on another part of it. After some time it gains high temperature which is called the plastic stage in which it is ready to be coalesced by applying sufficient and necessary pressure on both parts of the workpiece.
As no melting occurs in the friction welding process, so it is not included in the fusion welding process but mostly counted in the forged welding process. It is used with metals and thermoplastics in the construction of a wide variety of aviation and automotive applications.
History
The Soviet Union developed this welding process in 1956. The American companies Caterpillar, Rockwell International, and American Manufacturing Foundry, all have developed machines for this process.
Also Read:
- What is Electroslag Welding? – Complete Overview
- Electron Beam Welding Process – Equipments, Working Principle with Diagram
- How Submerged Arc Welding Works?
Working of Friction Welding
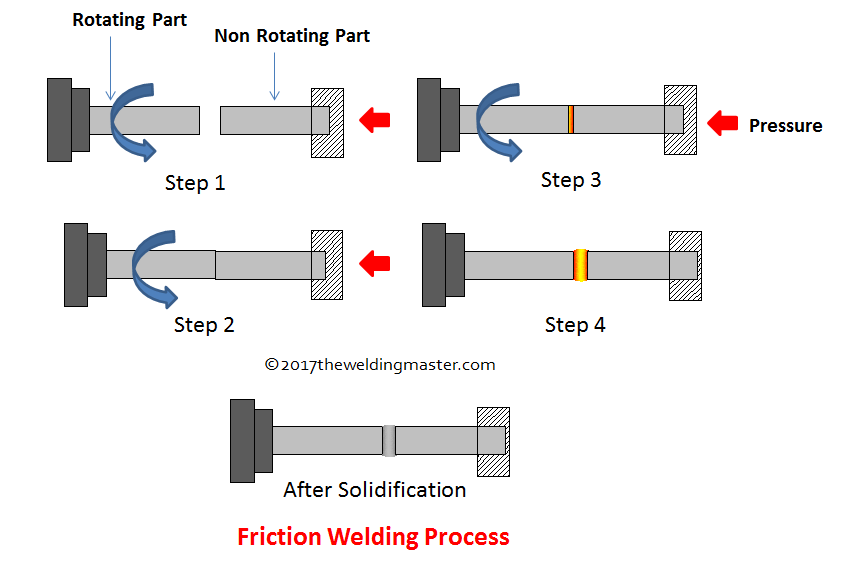
In this welding process, friction is used to generate heat at the interference surface. This heat is further used to join two workpieces by applying external pressure at the surface of the workpiece.
There are many techniques to perform friction welding, but the basic rule or principle remains the same which can be seen as follows:-
- Firstly one part of the workpiece is fixed on the chuck which is stationary and the other part is placed in the rotor.
Then the rotor is rotated at high speed with the help of an external power source. - Now a high pressure is applied on the stationary workpiece which rubs against the rotating workpiece and generates high friction. This friction generates heat at the contact of both the workpieces. It is applied until the plastic forming temperature is achieved.
- The rotor is stopped when the pressure is applied increasingly until the whole weld is formed.
For a Better Explanation Watch the Video Given Below:
Types of Friction Welding
There are many variations in the process which basically work on the same principle as mentioned above which are as follows:-
1. Continuous Induce Friction Welding:
In this welding process, the rotor is connected with a band brake. When the temperature reaches the limit of plastic temperature, then the band brake comes into action whose role is to stop the rotor but the pressure applied on the workpiece increases until the weld is formed.
2. Inertia Friction Welding/Spin Welding:
In this welding process, in place of the band brake, there are engine flywheel and shaft flywheel. These flywheels connect chuck to the motor. Firstly both flywheels are connected with each other. When the speed or friction reaches its limit, the engine flywheel gets detached from the shaft flywheel. Shaft flywheel has a low moment of inertia which stops automatically without any help of brake. The pressure force is continuously applied to the workpiece until the weld is formed.
Also Read:
- What is Flux Cored Arc Welding (FCAW)?
- Explosive Welding – Equipment, Types, Working, Advantages and Disadvantages with Application
- What is Plasma Arc Welding? – Complete Overview
3. Linear Friction Welding
This process is the same as the spin welding process but in this process, the chuck rotates circularly whereas in linear friction welding it oscillates instead of spinning. It has a much slower speed as compared to spin welding which is beneficial for the job in linear friction process because many times the quality of the weld is better than that of spin welding.
4. Linear Vibration Welding
In linear vibration welding, the materials are placed in contact with each other and put under high pressure. An external vibration force is then applied to rub the pieces against each other, perpendicular to the pressure being applied. Both the workpieces are vibrated at 200 Hz frequency. Mostly this technique is used in the automotive industry.
5. Friction Surfacing
This process is derived from a friction welding process where a coating material is applied to a substrate. Basically it is a surface coating process. A rod composed of the coating material which is called mechatrode. Then it is rotated under pressure, generating a plastic-type layer in the rod at the interface with the substrate. By moving a substrate across the face of the rotating rod a plastic-like layer is deposited.
Advantages
- It can produce high quality of welds in a short period of time.
- No filler metal and flux is used in this process.
- It consumes less time than any other process.
- In this process, less skill is required to use it.
- Less area is affected by the heat produced in the process.
- A wide variety of metals can be operated on this system.
Disadvantages
- This process is limited to angular and flat butt joints.
- The preparation of the workpiece is more critical than making a weld.
- The cost of the setup of the machine is very high.
- It can only be used for smaller parts of machines, big parts are not compatible with it.
Application
- It is used to make tubes and shafts.
- It is mostly used in aerospace, automobile, marine, and oil industries.
- Used in electrical industries for welding copper and aluminum equipment.
- It is used to weld Gear levers, drill bits, connecting rod, etc.
Reference: