Introduction:
Friction stir welding (FSW) is a solid-state joining process. Solid-state welding means that there is no molten state included in joining or welding the workpiece. This joining technique saves energy and is eco-friendly. It is mostly used to weld aluminum materials in the automobile and aerospace industries.
The FSW is the process in which a tool is used which does not gets consumed in joining the workpiece so it is called a non-consumable tool. A non-consumable rotating tool with a pin and a shoulder is inserted into the adjacent edges of sheets or plates to be joined and moved along the line of joint till the end. It is considered to be the most significant development in the metal joining process and is a “green” technology due to its energy efficiency, environment friendliness, etc.
History:
The Friction Stir Welding (FSW) process was invented by Wayne Thomas of the Welding Institute in 1991, at Cambridge, in the United Kingdom. TWI has further developed this process and patented it.
Principle of Friction Stir Welding
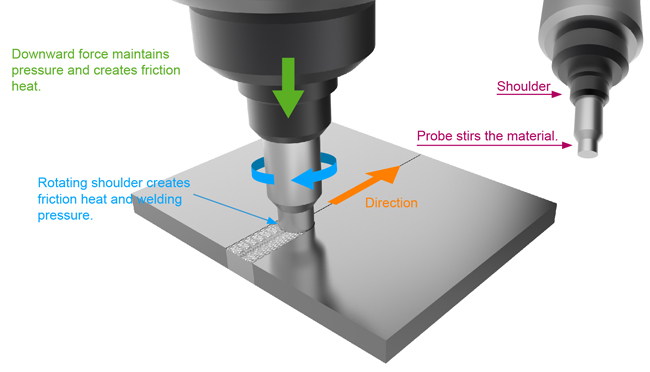
The adjacent metal sheets are joined by a tool that is non-consumable tool and is made up of a pin and a shoulder. The non-consumable tool used in friction stir welding performs two functions first it heats the workpiece to raise its temperature sufficiently to the stage at which it is not molten but plastically melted and second it moves along the edges of the workpiece to weld it or to make a joint.
The heating is achieved by friction between the tool and the workpiece and because of the plastic deformation of the workpiece. The localized heating softens the material around the pin and shoulder. The tool rotation leads to the movement of material from the front of the pin to the back of the pin. And this completes the welding and a strong solid-state joint is ready.
Working Process of Friction Stir Welding (FSW)
- Firstly clamp the workpiece in a heavy-duty setup, so that it does not move or shake at the time of welding.
- The workpiece should be abutting i.e. both parts should be kept side to side at a particular distance from each other.
- Now insert a blunt or probe tool till the whole pin gets inserted in the abutting edges.
- Now the shoulder gets in touch with the abutting edges.
- The tool starts rotating within contact with the job.
- Due to contact of the workpiece, friction is applied and as a result of it, heat is generated.
- This heat makes the metal plastically melt.
- When the metal gets plasticized the high downward forces or pressure makes a strong, clean and solid-state weld.
Also Read:
- Friction Welding Process – Working, Types, Advantages, Disadvantages with Application
- What is Electroslag Welding? – Complete Overview
- Top 8 Advantages of arc Welding
Important Welding Parameters:
Tool Design:
Tool design is a very important factor in improving the quality of the workpiece. To achieve a good finish in job the tool material should be sufficiently strong, tough and hard-wearing at the welding temperature. The tool should conduct less heat to decrease heat losses and minimizes the damage to the machine’s parts caused by the heat produced. The tool should be highly resistive to oxidation so that there are no traces of rust.
2. Tool Speeds:
As we know the friction stir welding process is a slower type of welding process, this is because the cylindrical tool turns on the joint to generate heat, and then moving along the length of the joint transmitting that heat. The probe tool with the cylindrical part rotates within the range of 200 to 2000 rotations per minute (rpm). The traverse rate of the tool along the joint line is between 10 to 500 millimeter per minute (mm/min).
3. Tool Tilt:
Tool tilt is also an important aspect to get a good quality of weld. It welds the joint in a slightly lean position or tilt position which is about 2 to 4 degrees. The forces applied downwards can affect the joint, so to prevent this condition a tilt is given.
4. Plunge Depth:
The plunge depth is the total depth till which the shoulder of the tool gets inserted into the metal sheet while the pin penetrates further than the shoulder. It is very important factor to determine the quality of job as the plunge depth needs to be correctly set because it ensures the necessary downward pressure is achieved and also ensure that the tool fully penetrates the weld because if the tool is not inserted to correct depth machine may deflect from its position. And on giving excessive plunge depth the job may have pin rubbing marks on it.
Also Read:
- What is Explosive Welding?
- What is Flux Cored Arc Welding (FCAW)?
- Laser Beam Welding – Equipment, Principle, Working with Advantages and Disadvantages
Advantages:
- Mechanical properties of the metal are not degraded after the welding process.
- There is no production of fumes and unwanted metal spatter of molten state.
- In the FSW process safety level is up to the mark and no risk of getting hurt.
- No consumable, no filler metal and no shielding gas is required in this process.
- It can be used in any position i.e.in horizontal, vertical etc.
- Friction stir welding is a “green” technology as it does not produces any health hazardous materials which may lead to destruction of the environment or people.
- It can be applied to various types of joints like lap joints, butt joints, T joints, and fillet joints.
- There is no requirement to clean the metal surface.
Disadvantages:
- The hole which is made by the blunt probe tool is left unfilled at the time of exit.
- Heavy-duty clamping setup is required to hold the workpiece or job during the welding process.
- Large downward forces are required to get the probe tool get inserted inside the metal.
- Many times this welding process is slower than many other processes.
- Friction stir welding cannot make weld joints in which there is requirement of metal deposition.
- The initial cost of the FSW machine is too high.
- It is less flexible than manual and arc welding processes
Application:
- Used in shipbuilding companies to weld big parts of the ship.
- Mostly used in aerospace industries to join or weld the bigger parts like wings etc.
- It is used in automotive industries to held many parts.
- Used in railways.
- It is also used in the fabrication work of metals.
Conclusion
In this post, we have discussed What is Friction Stir Welding, its working principle, advantages and disadvantages with application and video tutorials. I hope you have understood this topic more clearly without any doubt. If you found this piece of information useful and valuable then don’t forget to like and share it.