Explosive Welding (EW) is a solid state welding process i.e. this process does not include molten state during the welding of the different parts of metal which have to be welded. This method was developed in the decades after World War II. Dupont applied for the patent of this welding process in 1962 which was granted on June 23, 1964.
It is the process in which two or more dissimilar metals are joined by accelerating one part at high speed by the use of chemical explosions through controlled detonations or explosions. This welding is considered a cold welding process which allows metal to be joined without losing its pre-bonded properties. This process does not require any filler material to weld metals. This process is advantageous because it does not affect the properties of the metal and does not melt etc.
Working Principle:
Explosive welding is basically based on metallurgical bonding that is the bonds between dissimilar metals. In this process controlled explosions are done which generates a high quantity of pressure which results in deformation of metal workpiece plastically, this deformation results in metallurgical bonding between the metal parts. These detonations occur for a very short period of time due to which neither the metal gets damaged nor the properties of the metal get altered. The metallurgical joints or bonds are stronger than the original metal bonds.
Also Read:
- Top 8 Advantages of arc Welding
- Friction Welding Process – Working, Types, Advantages, Disadvantages with Application
- What is Seam Welding and How it Works?
Required Material and Equipment:
- Base plate (Backer): This plate remains stationary it provides support and it helps in reducing or minimizing the damage at the time of detonation.
- Flyer plate (Clad): This plate gets welded on the base plate. It is situated at the parallel of the base plate or at the angle at which the base plate is inclined.
- Standoff distance: It is a very important factor considered for EW. It is the distance between the flyer plate and the base plate. Generally, standoff distance is taken as double thickness of it.
- Buffer plate: This plate is used to reduce the effect of the explosion on the upper surface of the flyer plate. This protects the flyer plate from any damage due to explosion.
- Explosives: they are placed on the buffer plate or directly on the clad. It produces an explosion for the welding.
Types of Explosive Welding
Basically, it can be categorized into two categories on the basis of the apparatus set up for the process which is as follows:-
1. Parallel EW:
In this method of welding, thick and large plates are used and joined. There is a standoff distance between the plates.
2. Oblique EW:
In this process, the base plate is fixed and the flyer plate is inclined at an angle to the base plate. This setup is used to join small and thin plates.
Working of Explosive Welding
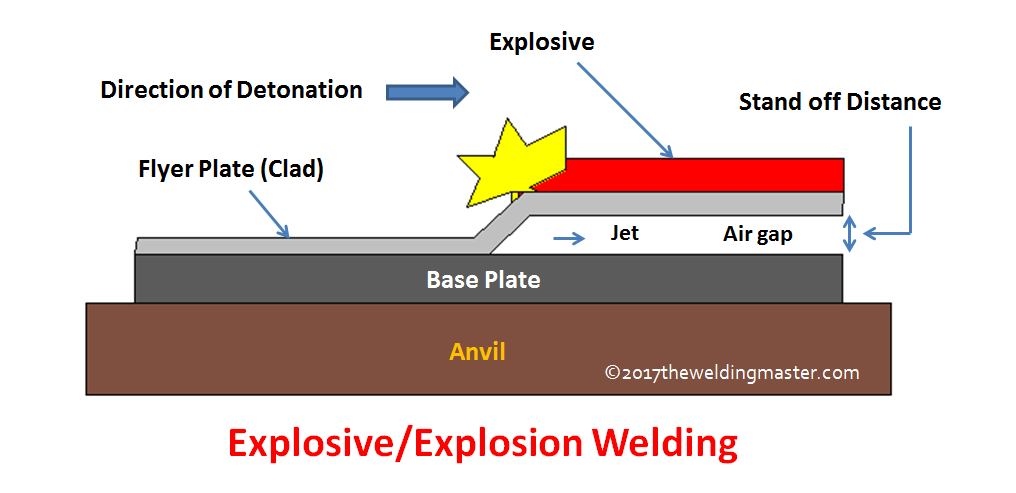
- Firstly the metal parts or plates should be cleaned thoroughly; no rust should remain on them which may lead to some problems in the welding process.
- Now according to the type of explosive welding, the setup should be kept as follows:-
- If it is parallel EW then the base plate and flyer plate will be parallel to each other as the name suggests.
- If it is oblique EW then the base plate has to be fixed on anvil and the flyer plate will make an angle according to the base plate.
- The prepared explosives are placed in a box of the same size as of surface to be welded which is placed over the buffer plate which protects the flyer plate below it.
- Now the explosives are ignited.
- On igniting the explosives, a high pressure is created which deforms the plates.
- These plates get plasticized and form metallurgical bonds which are stronger than the original metal bonds.
For a Better Explanation Watch the Video Given Below:
Also Read:
- What is Electroslag Welding Process – Principle, Main Parts, Working, Advantages and Disadvantages with Application
- What is Forge Welding and How it Works?
- What is TIG Welding Process or Gas Tungsten Arc Welding (GTAW)
Advantages
- It is able to weld many dissimilar metals, normally the metals which are not able to be welded by any other method.
- This process is very simple; no high skills are required to operate it.
- Extremely large surfaces can be bonded or welded.
- There is no effect on parent properties of the metal after welding, they are unchanged.
- A very small quantity of explosives is used in the explosive welding process.
- No part of the workpiece gets heated like in other methods of welding.
- In this process no molten state of metal is included; metal is only plasticized to join other part.
Disadvantages:
- It can weld only ductile metal with high toughness.
- The geometries welded are limited to simple designs– flat, cylindrical, and conical.
- Higher safety precautions are involved due to the explosives used.
- The use of explosives in industrial areas will be restricted by the noise and ground vibrations caused by the explosion.
Applications:
- It is used to weld large structure sheets of aluminium to stainless steel.
- It is used to weld cylindrical components like pipes, concentric cylinders, tubes etc.
- Welds clad sheet with steel in a heat exchanger.
- Join dissimilar metals which cannot be welded by other welding processes.
- For joining cooling fan etc.
- Joining of pipes and tubes.
- Joining of dissimilar metals can be done for eg – Aluminium to steel, Cu to stainless steel, Titanium alloys to Cr – Ni steel, Tungsten to Steel, etc.
Conclusion
In this article, you have learned about what is Explosive Welding (EW) and how it works. If you found this article informative and useful then don’t forget to like and share it.