Electroslag Welding Process is a process in which the job is welded through the molten slag covering which is a result of a high quantity of heat which is generated by the circulation of electric current through the electrode and the job.
- Robert K Hopkins discovered this welding process in February 1940 at Paton Institute, Kiev, USSR.
- This welding process is a single pass high productive welding process that is used for welding thick (25-300 mm) materials in vertical or close to vertical positions.
Principle of Electroslag Welding:
The electroslag welding process works on the principle of heat generation due to arc and electric resistance. An arc is made between the welding electrode and the workpiece which starts melting the filler metal to fill the filler cavity. Now the heat is produced due to electric resistance when the current passes through the surface. The heat further starts melting the filler metal which is continuously fed from the roller. This filler wire melts and fills the weld and makes it a strong joint.
Also Read:
- What is Flux Cored Arc Welding (FCAW)? – Complete Overview
- What is Underwater Welding and How it works?
- What is Plasma Arc Welding? – Complete Overview
Equipments or Main Parts
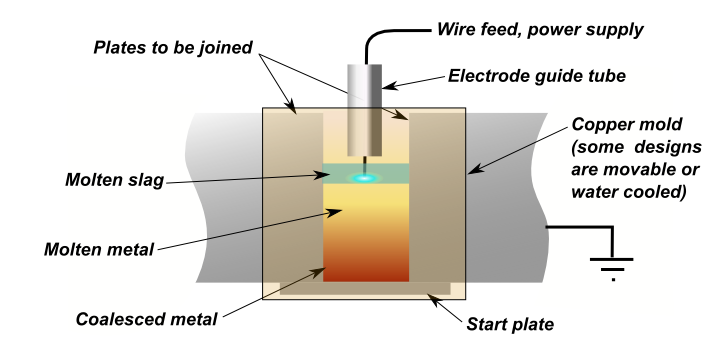
1. Electrodes:
Generally, two types of electrodes that are solid and metal-cored are used. Solid electrodes are more popular than metal-cored electrodes.
2. Flux:
Flux is the most important consumable material of Electroslag Welding. In its molten state, it transforms the electrical energy into heat energy which helps in melting the electrode wire and the base metal to form a weld joint. It is also required to protect the molten weld metal from the atmosphere and to ensure stability. The flux in its molten state is required to conduct electricity but at the same time, it should offer sufficient resistance to its flow for generating enough heat to do welding.
Arcing results when the resistance is less than the minimum required quantity. The slag must also have minimum viscosity so that it does not be too thick to stop good circulation and nor too thin to result in excessive leakage.
3. Electrode Guide Tube:
It is used to guide the electrode wire at the desired position where the welding is to be done.
Working of Electroslag Welding
It works as follows:
- Firstly current flows from the welding electrode to the base plate. This establishes an arc between electrode and base plate which heats the flux. This heat which is produced during arc formation results in melting the filler metal and deposits into the weld cavity.
- Now the cooled copper shoe starts its function of solidifying the filler metal into the weld cavity. This is done to avoid the flowing of weld metal outside.
- As the filler metal solidifies into the weld cavity, the current flows through it. Then it generates heat due to electric resistance. This heat is further used to continue the melting of the filler metal into the weld cavity. Which means that heat is regenerated, which results in less waste of heat or energy.
- Roller arrangement continuously provides the filler metal.
- During the welding of the metals, both the copper shoe and feed mechanism move upward until the whole cavity is formed.
- This will create a strong joint in a single pass. The single or multi-pass weld is used according to plate thickness.
Also Read:
- Top 5 Best Welding Boots for Welders
- What is TIG Welding Process or Gas Tungsten Arc Welding (GTAW)
- What is MIG Welding Process or GMAW (Gas Metal Arc Welding)?
Advantages:
- The cooling rate is very low so there is no problem of cold cracking.
- There is no problem of slag inclusion or porosity.
- The process is semi-automatic and faster.
- The heavier section can be welded in a single pass.
- High productivity can be achieved.
- Low cost for joint preparation.
Disadvantages:
- Too high heat input to base.
- High temperature of welding needs cooling arrangement.
- Slow rate of cooling give columnar grain in weld.
- When the heat input is very high then the weld quality can be poor, including low toughness caused by the coarse grains in the fusion zone and the heat-affected zone.
- In Electroslag welding, it has some tendency towards hot cracking and notch sensitivity in the heat affected zone.
- It is restricted to vertical position welding, because of large molten metal pools and slag.
- It is difficult to close cylindrical welds
- It tends to produce large grain sizes..
- If you are creating joints below 60 mm then Submerged Arc Welding (SAW) is more economical than electroslag welding process.
Application:
- It is used in heavy industries where plate thickness is up to 80 mm to be joined.
- Welding of thick walled large diameter pipes is done by this welding process.
- Welding of storage tanks is done by it.
- It is used to construct big and thick parts of ships.
Conclusion:
In this post, we have discussed what is electroslag welding, its main parts, working, advantages, and disadvantages with application. If you found this piece of information valuable and useful then don’t forget to like and share it.