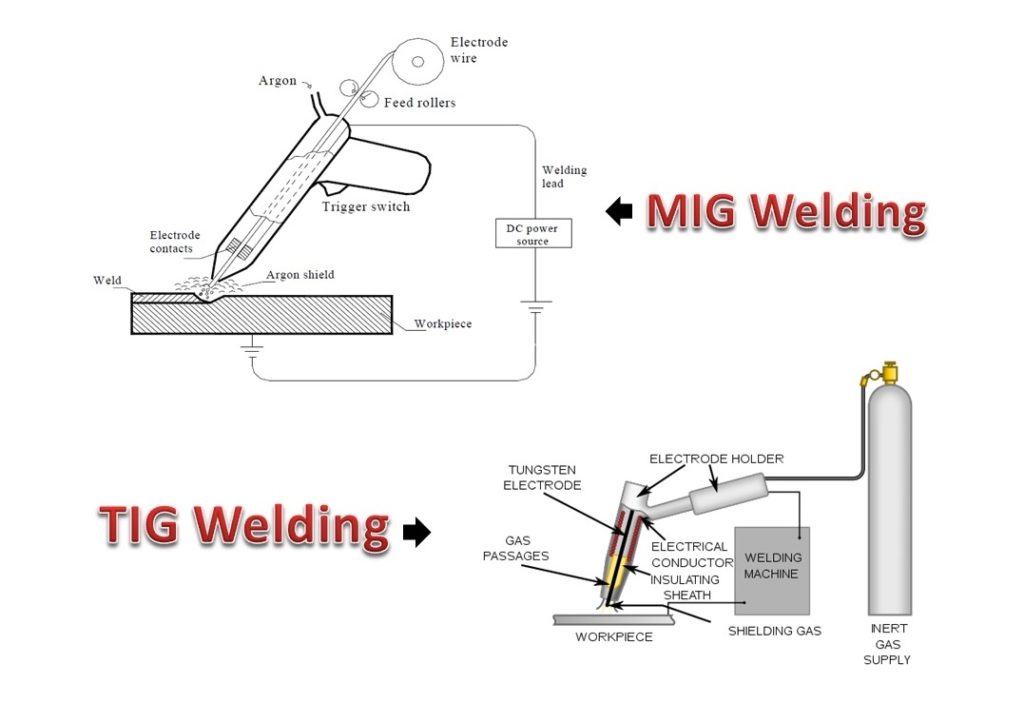
When it comes to welding, two of the most popular and versatile techniques are MIG (Metal Inert Gas) and TIG (Tungsten Inert Gas) welding. Each method has unique advantages and specific use cases, making the choice between them dependent on the nature of your project. In this guide, we’ll break down everything you need to know about MIG vs TIG welding, including their differences, strengths, limitations, and the types of materials and applications they’re best suited for.
What is MIG Welding?
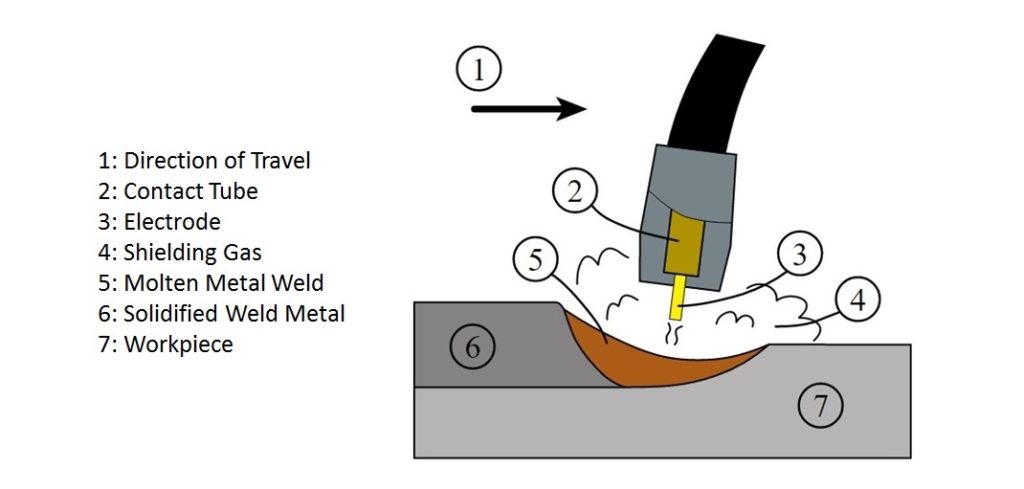
MIG welding, also known as Gas Metal Arc Welding (GMAW), uses a continuous wire feed as both the electrode and filler material. In this method, a shielding gas, usually argon, carbon dioxide, or a mix of both, is used to protect the weld from contaminants in the air. MIG welding is popular because it’s straightforward, efficient, and suitable for various materials.
Key Characteristics of MIG Welding:
- Speed: MIG welding is faster than TIG welding due to its continuous wire feed.
- Ease of Use: This technique is user-friendly, even for beginners, as it requires less skill and has a shorter learning curve.
- Versatility: MIG welding is versatile and works well on thick materials like mild steel, aluminum, and stainless steel.
- Minimal Cleaning Required: With MIG welding, there’s typically less splatter and minimal post-weld cleaning.
Common Applications for MIG Welding:
- Automotive Repair: The speed and efficiency make it ideal for auto repair.
- Construction and Structural Projects: MIG welding is frequently used for constructing steel frames, bridges, and other heavy-duty structures.
- Manufacturing and Fabrication: It’s widely used in factories due to its suitability for high-speed production lines.
What is TIG Welding?
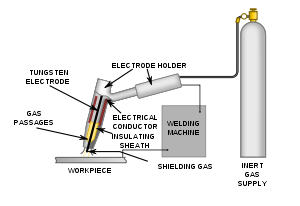
TIG welding, or Tungsten Inert Gas Welding (also called Gas Tungsten Arc Welding, or GTAW), uses a non-consumable tungsten electrode. The welding process is slower because the welder must feed filler material into the weld pool manually. However, TIG welding provides high precision and clean welds, which are essential for specific applications and delicate work.
Key Characteristics of TIG Welding:
- Precision and Quality: TIG welding provides a highly controlled arc, allowing for superior quality welds.
- Versatility with Materials: TIG welding can be used on a variety of materials, including thinner metals and metals with low melting points.
- Skill Level: TIG welding requires more skill and experience, as the manual feeding of filler material requires steady hands and coordination.
- Clean Welds with No Splatter: The clean finish of TIG welding is ideal for jobs that demand a polished look, as it produces minimal splatter.
Common Applications for TIG Welding:
- Aerospace and Aviation: Due to its precision, TIG welding is common in aerospace applications where weld quality is paramount.
- Artistic Welding and Sculpture: The clean, fine welds are ideal for creating detailed metal art pieces.
- Food and Beverage Industry Equipment: Stainless steel components used in food and beverage processing require high-quality, hygienic welds, often made with TIG welding.
MIG vs TIG Welding: Key Differences
Feature | MIG Welding | TIG Welding |
Ease of Use | Easier, beginner-friendly | More challenging, requires skill |
Welding Speed | Faster due to continuous wire feed | Slower, due to manual feeding of filler |
Material Thickness | Best for thicker materials | Ideal for thin and delicate materials |
Precision | Moderate, good for general purposes | High precision, suitable for intricate work |
Splatter | Low to moderate splatter | Minimal to no splatter |
Cost | More affordable and accessible | Equipment is more costly |
Difference Between MIG And TIG Welding: Pros and Cons
MIG Welding Pros:
- Faster Process: The continuous wire feed means the welding process is faster and suitable for larger projects.
- Easier to Learn: MIG welding has a short learning curve, making it accessible for beginners.
- Affordable Equipment: MIG welding machines are typically less expensive and widely available.
MIG Welding Cons:
- Less Precision: MIG welding isn’t ideal for intricate, detailed welds.
- More Maintenance: Because of the electrode wire, there’s more splatter, and frequent tip and liner replacement may be necessary.
TIG Welding Pros:
- High-Quality Welds: The precision of TIG welding produces clean, strong welds with little to no splatter.
- Versatile Material Use: TIG welding can be used on a variety of metals, including aluminum, stainless steel, and even thin materials.
- No Consumable Electrodes: Unlike MIG welding, TIG welding doesn’t require consumable electrodes, reducing waste.
TIG Welding Cons:
- More Complex to Learn: The manual feeding of filler material and handling of the torch requires skill and experience.
- Slower Process: TIG welding is slower, making it less ideal for high-speed, large-scale projects.
- Higher Cost of Equipment: TIG welders and materials are generally more expensive than those used in MIG welding.
MIG vs TIG Welding: Choosing the Right One for Your Project
Consider the Material Type and Thickness: If you’re working with thick materials like steel or aluminum, MIG welding might be more effective. However, for thinner or delicate metals, TIG welding’s precision is invaluable.
Project Size and Speed Requirements: For large projects requiring speed, such as in manufacturing or construction, MIG welding’s efficiency makes it the better choice. For small, intricate projects, TIG welding’s precision is worth the extra time and effort.
Skill Level and Experience: Beginners may find MIG welding more manageable, while TIG welding is recommended for experienced welders due to its complexity and required precision.
Desired Aesthetic and Weld Quality: If the project requires a clean, polished finish with no splatter, such as in art or high-precision industries, TIG welding is superior.
MIG vs TIG Welding: Final Verdict
Both MIG and TIG welding have unique strengths, making them valuable for specific applications. MIG welding is fast, versatile, and accessible, making it ideal for large-scale, heavy-duty projects. In contrast, TIG welding offers precision and clean finishes, perfect for projects demanding high-quality welds on thin or delicate metals.
Conclusion
In the debate of MIG vs TIG welding, there’s no one-size-fits-all answer. Your project requirements, skill level, and the type of materials you’re working with should guide your choice. By understanding the differences and advantages of MIG and TIG welding, you can select the welding technique that aligns best with your goals and produces the highest quality results.