The Electron Beam Welding Process is a fusion welding process in which a high-velocity electron beam is used to join two metals together. The high-velocity electron beam when strikes the weld area of two metal pieces and very intense heat is generated which melts the metal and they fuse together to form a strong weld. The whole process is carried out in a vacuum chamber to prevent it from contamination.
It was developed by the German physicist Karl-Heinz Steigerwald. In 1958 he introduced the first practical EBW machine that was put into operation
Working Principle
It works on the principle that when a high-velocity beam of electron that has Kinetic energy strikes the two metal pieces, the kinetic energy of the electron transformed into heat. The intensity of heat produced is so much that it melts the two metal pieces and fuse them together to form a strong weld.
Main Parts of EBW
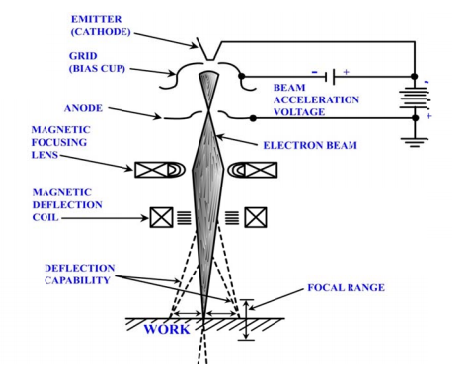
The various Equipment of Electron beam welding is
1. Electron Gun
It is used to generate, accelerate, and align the electron beam in a desired direction and spots on the w/p. There are two types of electron guns, the first one is self-accelerated and the second one is work-accelerated.
- In self self-accelerated gun, the acceleration of electrons takes by applying a potential difference between the cathode and anode.
- In the work accelerated gun, the acceleration of the electron takes place by applying the potential difference between the cathode and the workpiece. The workpiece (w/p) acts as anode.
The main parts of an electron gun are:
(i) Cathode (Emitter or Filament): It emits the electron.
(ii) Anode: It is a positively charged Electrode and attracts the electron produced by the cathode. It accelerated the electrons under the influence of high potential difference. For high voltage equipment, the potential difference ranges from 70 kV to 150 kV, and for small-voltage equipment it ranges from 15 – 30 kV
(iii) Grid Cup: It is used to control the electron beam. It stops the divergence of electrons produced by the cathode. It has applied with negative voltage with respect to the cathode.
(iv) Focusing Unit: Tt consists of two parts – a magnetic lens and a deflector coil. The magnetic lens focuses the electron beam on the w/p. And the deflector coil is used to deflect or guide the beam to the desired locations. The extent of deflection can be varied by changing the amount of dc voltage across the deflector plate.
Also Read:
- What is Underwater Welding and How it works?
- Explosive Welding – Equipment, Types, Working, Advantages and Disadvantages with Application
- Ultrasonic Welding Process – Working Principle, Parts, Advantages and Disadvantages with Application
2. Power Supply
The power supply used in the Electron Beam Welding process is DC power supply sources. The voltage ranges from 70-150 kV for high voltage equipment and 5-30 kV for small voltage equipment. The current level ranges from 50 to 100 mA.
3. Vacuum Chamber
It is a chamber in which the vacuum is created by the vacuum pump. Roughing mechanical pump and diffusion pump is used to create a vacuum in the vacuum Chamber. The pressure ranges from 100 kPa for open atmosphere to 0.13-13 Pa for partial vacuum and 0.13 to 133 mPa for hard vacuum. The extent of scattering increases with the increase in the vacuum and this allows more penetration in the workpiece.
4. Work Handling Devices:
The fixtures are used to hold the workpiece. The workpiece motion is controlled by the CNC (Computer Numerical Control).
Working of Electron Beam Welding Process
- In Electron Beam welding, the electron is produced by the cathode of the electron gun.
After cathode, a cup grid is provided. It prevents the divergence of electron and control it. - Because of the high voltage applied across the cathode and anode. The anode which is positively charged attracts the electron from the cup grid.
- The anode accelerates the electron and its velocity increases and reaches the range of 50000 – 200000 km/s. From the anode, the high-velocity electron beam is passed through the magnetic lens and deflector coils.
- The magnetic lens focuses the electron beam to the desired location on the workpiece. And the deflector coil deflects the beam to the required weld area. As the high-velocity electron beam strikes the workpiece, intense heat is produced and it melts the metal of the two workpieces and fills the weld area. The molten weld solidifies and forms a strong weld joint.
Advantages
- High welding speed.
- Welding of dissimilar metals can be done.
- High weld quality and precision.
- Less operating cost.
- Materials with high welding temperatures can be welded easily.
- Less distortion due to less affected heat zone.
- The cost of cleaning is negligible.
- It welds thicker sheets, ranging from .025 mm to 100 mm.
- It is capable of welding inaccessible joints.
Disadvantages
- The cost of equipment is very high.
- A highly skilled operator is required to operate it.
- A high vacuum is required.
- Due to operation in a vacuum, large jobs can not be welded.
- High safety measures are needed to work with it.
Electron Beam Welding Applications
- It is used in aerospace industries for manufacturing jet components, parts of structures, transmission parts, and sensors.
- It is used in power generation industries.
- It is used in space industries to build titanium tanks and sensors.
- It is used in automobile industries to manufacture transmission systems, gears, and turbochargers.
- It is used in electrical and electronic industries to manufacture parts of copper structures.
- The other areas where it is used are nuclear industries, medical, research centers, etc.
Conclusion
Here we discussed what is electron Beam Welding, its main parts, working principle, advantages, and disadvantages with application. I hope you have understood it clearly and if you found this piece of information valuable and useful then don’t forget to like and share it.