Introduction
In the welding process, the metal pieces are joined together with the help heat of the arc. The heat of arc melts the metals of both pieces and fuses them to form a strong weld after solidification. Now the solidified fused metal formed after solidification is called welds. The welds formed can be of fillet, groove, slot, plug, seam, Flash, surfacing, and Spot type. In this post, we will learn about filled Weld in Details with its definition, parts, symbols, types, and features. So lets begin our study…
What is a Weld?
When two metal pieces are joined together with the help of any types of welding like arc welding, gas welding, etc, the metal deposits at the joints of the two pieces and gets solidified, the solidified metal part is called a weld.
What is a Fillet Weld?
When two metal pieces are joined together by keeping them perpendicular to each other or at an angle less than 180 degree, the weld at the joint formed is called Fillet Weld.
The fillet weld formed is triangular in shape and can have a flat, concave or convex surface. The flat, concave or convex shape of the weld depends on the technique used by the welder.
Fillet welds are commonly known as T joints and lap joints.
T joints: In T joints The two metal pieces are perpendicular to each other
Lap Joints: In Lap Joints the two metal pieces overlap with each other and welding is done at the edges.
Parts of Fillet Weld
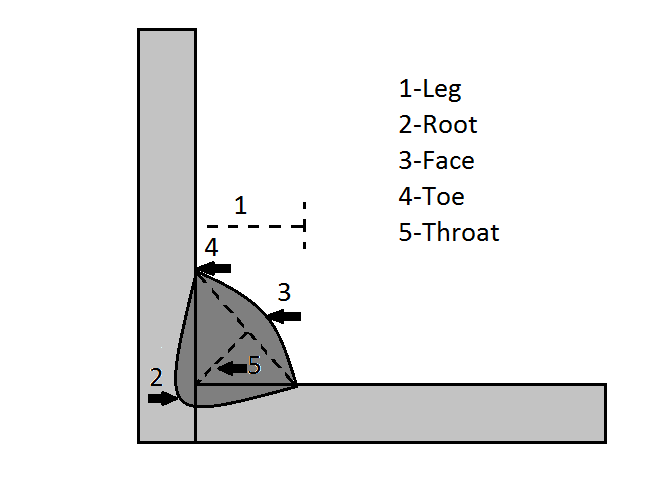
A fillet weld has five parts and These are
- Leg: After hypotenuse, the other two sides are the legs of the fillet weld.
- Root: The part that goes deepest penetration during welding is called root. It is the opposite angle of the hypotenuse in a triangular shape weld.
- Face: The hypotenuse of the triangular weld is called the face of the fillet.
- Toe: The end points of hypotenuse is the leg of the fillet.
- Throat: The distance from the root to the center of the face of the weld is called the throat.
Filet Weld Symbols
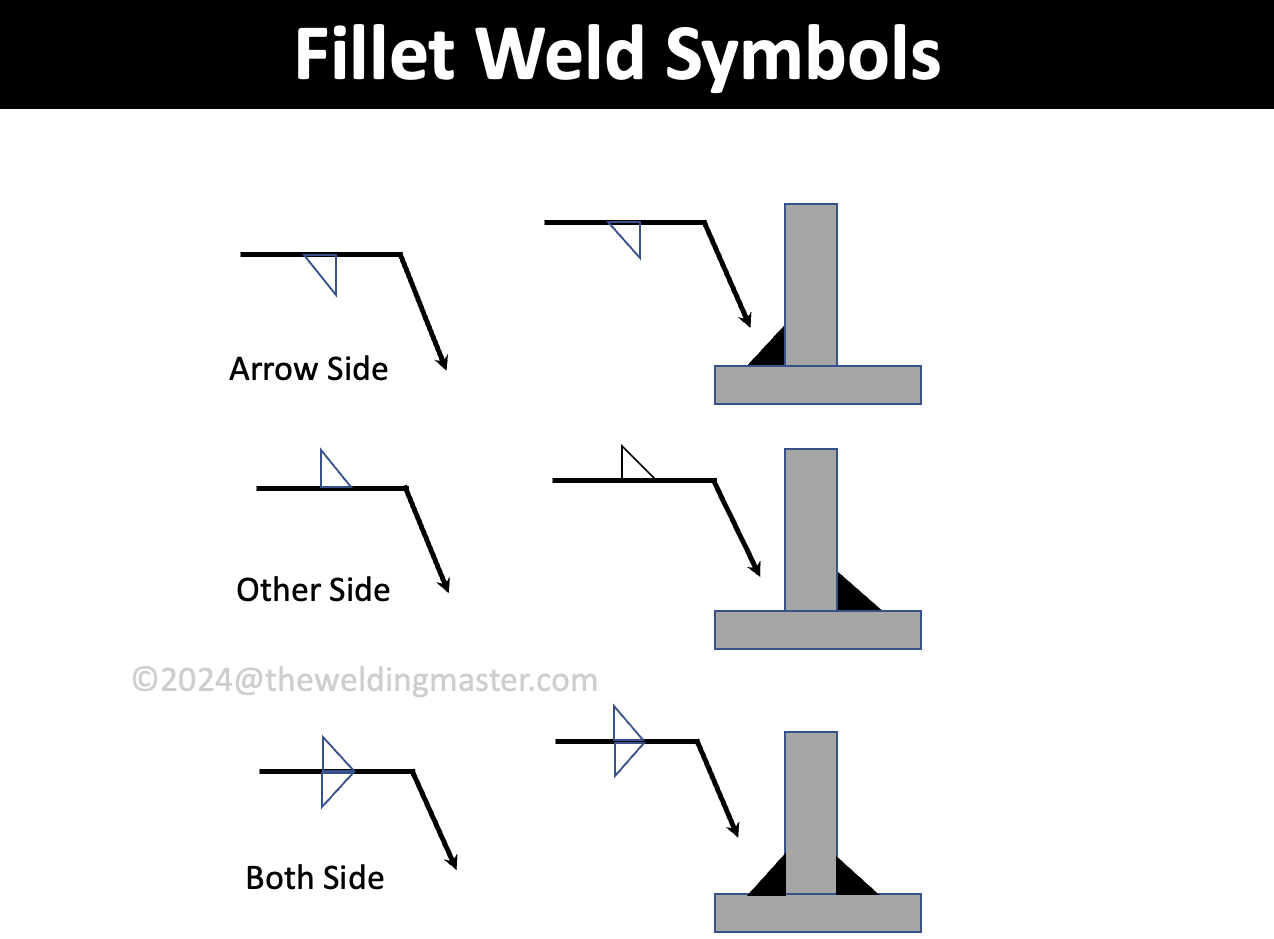
Types of Fillet Weld
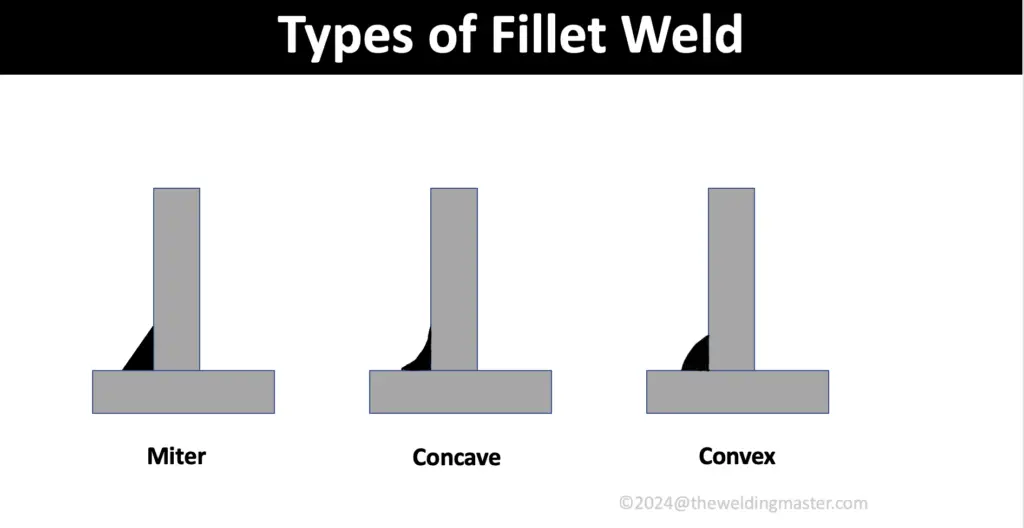
On looking at the faces of the triangular weld, It can be divided into flat, concave, and convex types of fillet weld.
Type of Fillet Weld | Description |
Falt or Mitre | The face of the weld is Flat. |
Concave | The face is in a Concave Shape. |
Convex | The face is in Convex Shape |
Features of Fillet Weld
Fillet welds are a cornerstone in the welding industry, known for their versatility and efficiency in joining metal components. Understanding the key features of fillet welds can help both novice and experienced welders achieve better results in their projects.
1. Triangular Cross-Section
One of the most distinctive features of a fillet weld is its triangular cross-section. This shape is formed as the weld metal fills the space between two intersecting surfaces, typically at a 90-degree angle. The triangular profile ensures a good distribution of stress and contributes to the strength of the joint.
2. Variety of Joint Configurations
Fillet welds can be applied to a variety of joint configurations, making them highly versatile. Common configurations include:
- T-Joints: Where one piece of metal is perpendicular to the other, forming a “T” shape.
- Lap Joints: Where two pieces of metal overlap each other.
- Corner Joints: Where two pieces of metal meet at a corner, forming an “L” shape.
- Skewed Joints: Where the angle between the pieces is not 90 degrees, requiring a skewed fillet weld.
3. Ease of Application
Fillet welds are generally easier to apply than other types of welds, such as groove welds, because they do not require extensive edge preparation or precise alignment of the parts to be joined. This ease of application makes fillet welds accessible for beginners and efficient for experienced welders.
4. Minimal Penetration Requirements
Unlike some welding techniques that require deep penetration into the base metals, fillet welds typically involve welding along the surface where the two metals meet. This reduces the amount of heat and energy needed, minimizing the risk of warping or distortion in the materials being joined.
5. Flexibility in Welding Positions
Fillet welds can be performed in various positions, including horizontal, vertical, overhead, and flat positions. This flexibility is crucial for many applications, particularly in construction and fabrication, where the position of the workpiece cannot always be controlled.
6. Cost-Effective
Fillet welds are often more cost-effective compared to other types of welds. The reduced need for edge preparation and lower heat input requirements result in faster welding times and lower material costs. This efficiency translates to savings in both labor and materials.
7. Strength and Durability
When done correctly, fillet welds provide strong and durable joints. The weld metal fills the corner between the pieces, creating a robust connection that can withstand various types of stress and loading conditions. This makes fillet welds suitable for structural applications where joint integrity is critical.
8. Inspectability
Fillet welds are relatively easy to inspect for quality. Visual inspection can often identify common issues such as cracks, porosity, undercuts, or lack of fusion. Additionally, non-destructive testing methods, such as magnetic particle testing or ultrasonic testing, can be used to ensure the weld meets the required standards.
9. Adaptability to Different Welding Processes
Fillet welds can be performed using various welding processes, including:
- Shielded Metal Arc Welding (SMAW): Commonly known as stick welding.
- Gas Metal Arc Welding (GMAW): Also known as MIG welding.
- Gas Tungsten Arc Welding (GTAW): Also known as TIG welding.
- Flux-Cored Arc Welding (FCAW): Similar to MIG welding but uses a flux-cored wire.
This adaptability allows welders to choose the best process for their specific project requirements, whether they prioritize speed, precision, or ease of use.
Conclusion
Fillet welds are a fundamental welding technique, prized for their versatility, ease of application, and cost-effectiveness. Their ability to create strong, durable joints in various configurations and positions makes them indispensable in many industries. By understanding the key features of fillet welds, welders can better appreciate their utility and apply them effectively in their work, ensuring high-quality results in every project.